Hey folks, I’m John P., founder of Texas Metal Works. In case I get hit by a bus one day I wanted to share as much as I can about welding tables, in the hope it helps you understand all the differences in the market, and how to decide what’s right for your particular situation. I don’t care what you buy, or where you buy it as long as you get what’s best for YOU! 🙂
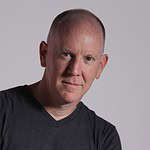
I’d like to make the point that this isn’t written by a ghost writer, an AI, or a marketing department. You’re getting my general overview based on years of running one of the biggest welding table manufacturers around…
Sorry, but this is a LONG somewhat dry document. Don’t read it after a big meal! Feel free to expand the Table of Contents and jump right to a section if it sounds like what you’re looking for. If you’re ready – let’s do this…
Evaluation Criteria
Before we get into all the variables associated, let’s first discuss the characteristics I would personally be focused on to evaluate welding tables.
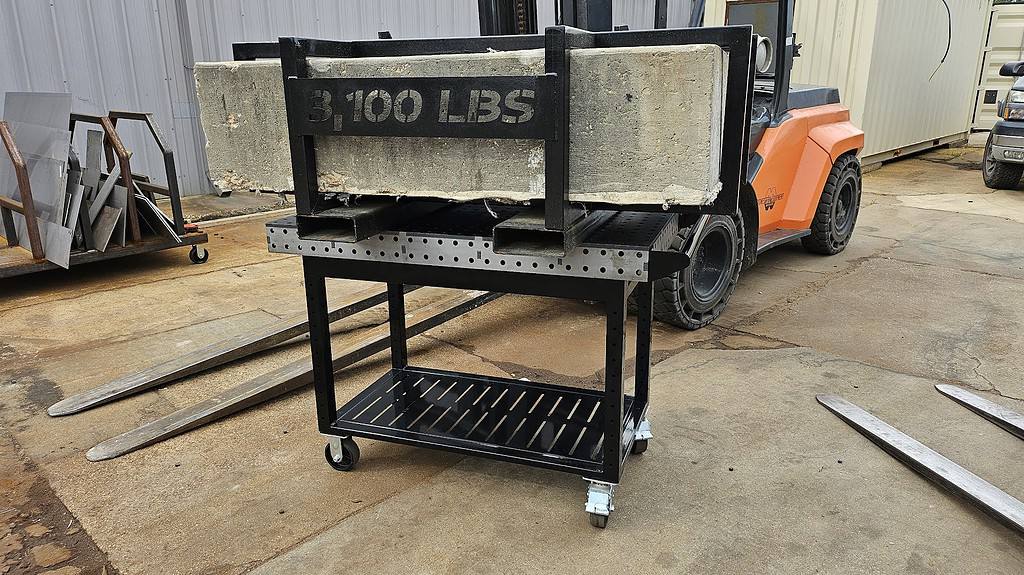
- Strength: A welding table should be capable not only of holding the weight of the workpiece, but of doing so with minimal deformation. The rated weight capacity of a table is not a good indicator since a table that is rated to hold 1,000 pounds doesn’t declare how much it flexes while doing so.
- Stability: This is very different from strength, but equally critical! The table needs to resist lateral forces so that it doesn’t buckle and injure someone. This is highly dependent not only on the design of the table top, but also the legs and other support infrastructure.
- Surface flatness: The table surface should be flat and even to ensure accurate and consistent results. A warped or uneven surface leads to distortion in the welded components, and extra cost to fix problems or scrap them and start over. However, increasing flatness drives up cost exponentially!
- Material quality: Welding tables are typically made from steel though there are some other common materials which I’ll outline later. The actual quality of the material is important for safety and predictability, as well as thickness to ensure enough mass to resist warping or deforming from the heat generated by welding.
- Size: You have to choose a table that will accomodate all of the projects you may need to build on it. In many cases you’ll also need to consider what kind of extensions are required, or how to configure multiple tables to act as a single large work surface.
- Adjustability and versatility: Some welding tables offer adjustable heights or modular designs that allow you to customize the table to suit your specific needs.
- Clamping and fixturing options: Look for tables with built-in clamping points or holes that allow you to easily secure your workpieces in place during welding.
- Portability: If you need to move your welding table frequently, consider factors such as weight and the presence of wheels or casters for easy transport.
- Price and value: Consider your budget and look for a welding table that offers the best combination of quality, features, and affordability for your needs.
Materials
Welding tables should be made out of metal, since welders need to be able to clamp the ground of their welding machine to the table in order for electricity to flow through the table, and through their parts while welding. The two general exceptions to this are laser welding, and oxy fuel welding, both of which are fairly rare at the moment.
Although welding tables can technically be made from almost any metal, primarily they will be made from carbon steel, cast iron, stainless steel, or aluminum – in that order, and with stainless and aluminum being rare. Each material has certain advantages and disadvantages.
Carbon Steel
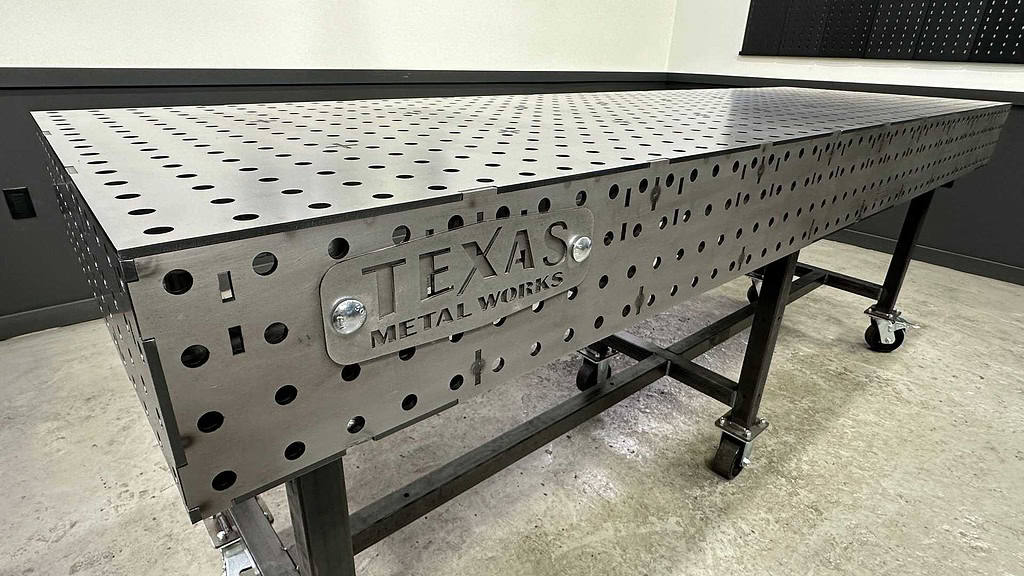
Advantages
- Carbon steel welding tables are generally lighter in weight compared to cast iron tables of similar sizes. This makes them more portable and easier to move around the workshop.
- Carbon steel is generally more affordable and widely available compared to cast iron, making it a cost-effective option for welding tables.
- Steel, especially from North America, Japan, Europe and Korea, can be purchased in specific blends, rendering consistent and reliable results.
- Carbon steel offers excellent strength and durability. It can withstand heavy loads and impacts, making it suitable for demanding welding applications.
- Carbon steel has a relatively high thermal conductivity, which means heat can dissipate quickly during welding. This helps reduce heat buildup and minimizes distortion in the welded components.
- Extremely easy to repair or modify. If a table is dented or damaged it can often be repaired by simply using filler weld and then sanding. And of course it’s simple to weld or bolt things on if you need to.
Disadvantages
- While carbon steel can withstand the heat associated with welding, excessive heat can lead to warping or distortion of the table surface over time. Thicker surfaces provide more mass to deal with the heat, or a simple technique to prevent heat buildup is to use spacers to keep work from directly touching the table surface.
- Welding stainless steel on a carbon steel table may lead to carbon contamination, which can affect the corrosion resistance and appearance of the welded stainless steel parts. Again, spacers can mitigate this issue to keep stainless from coming in contact with the weld surface.
- Untreated steel is susceptible to rust and corrosion if not properly maintained or coated. Certain treatments can provide semi-permanent protection, but using products such as oil or anti-spatter fluids are necessary to keep it looking new forever.
Cast Iron
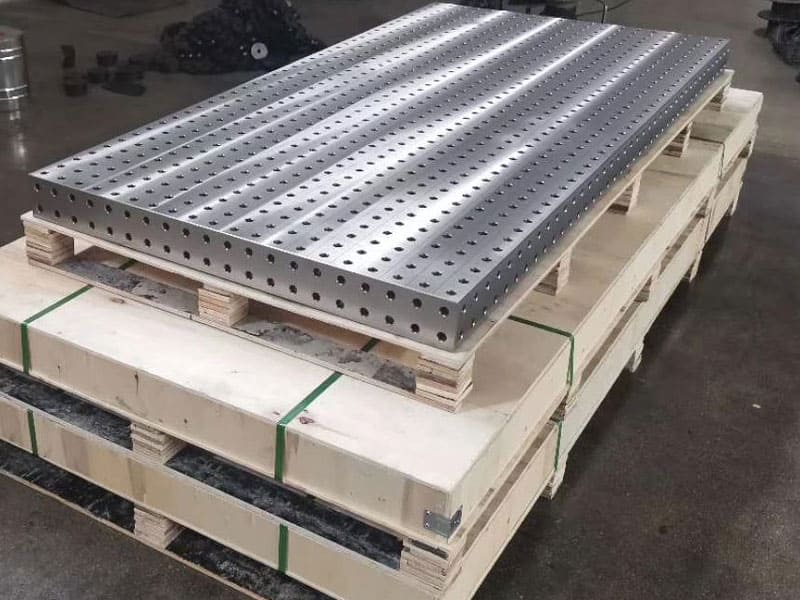
Advantages
- Cast iron offers excellent surface flatness and stability after machining, which is crucial for precision welding. Its density and the sheet mass employed minimizes table warpage or distortion under heat, maintaining a flat work surface.
- Cast iron welding tables are naturally self-dampening and provide excellent stability due to their high mass and density. They’re less susceptible to vibrations and distortions during welding.
- Cast iron is also known for its strength and durability, particularly in compression.
- Cast iron has better natural corrosion resistance than carbon steel, but it’s still prone to rusting if not properly maintained, especially in damp environments.
Disadvantages
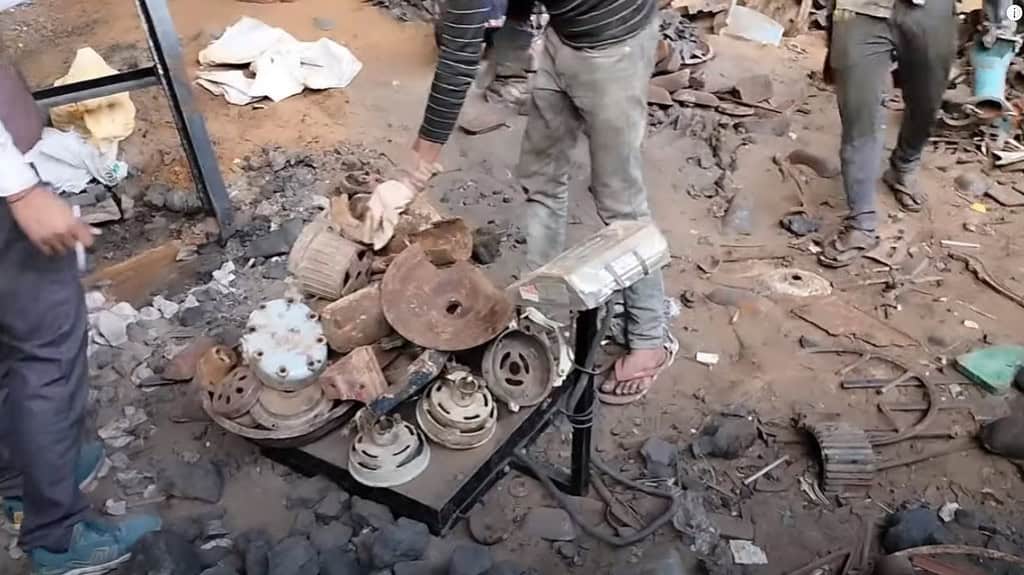
- Despite its durability, cast iron is more brittle than carbon steel. If a cast iron welding table is dropped or struck hard, it might crack or break. This is why cast iron tables often utilize a heavy steel base.
- If a cast iron welding table sustains damage, such as cracks or breaks, it can be challenging or impossible to repair.
- Cast iron has a lower thermal conductivity compared to carbon steel. It retains heat longer, which can be advantageous in certain welding applications where consistent heat is required, however generally welders prefer a welding table to act more as a heatsink to dissipate heat quickly.
- Cast iron welding tables are typically more expensive due to the specialized manufacturing process and the material’s inherent properties.
- Cast iron welding tables are significantly heavier due to the density of the material, which makes them much less portable and more challenging to relocate.
- If stainless steel is welded on a cast iron table, there’s a risk of iron particles transferring to the stainless, which compromises corrosion resistance and leads to rusting or discoloration.
- Cast iron commonly contains gas porosity or shrinkage cavities that form during the casting process. These pores or voids can weaken the structure of the welding table and affect its performance. They can also leave unattractive pockets on the surface.
- In countries like India, China and others cast iron is usually made from “mystery metals”. A quick search on YouTube will reveal some enlightening videos.
- Drilling, cutting, or welding modifications to a cast iron table can be difficult and may compromise its strength and integrity.
Stainless Steel
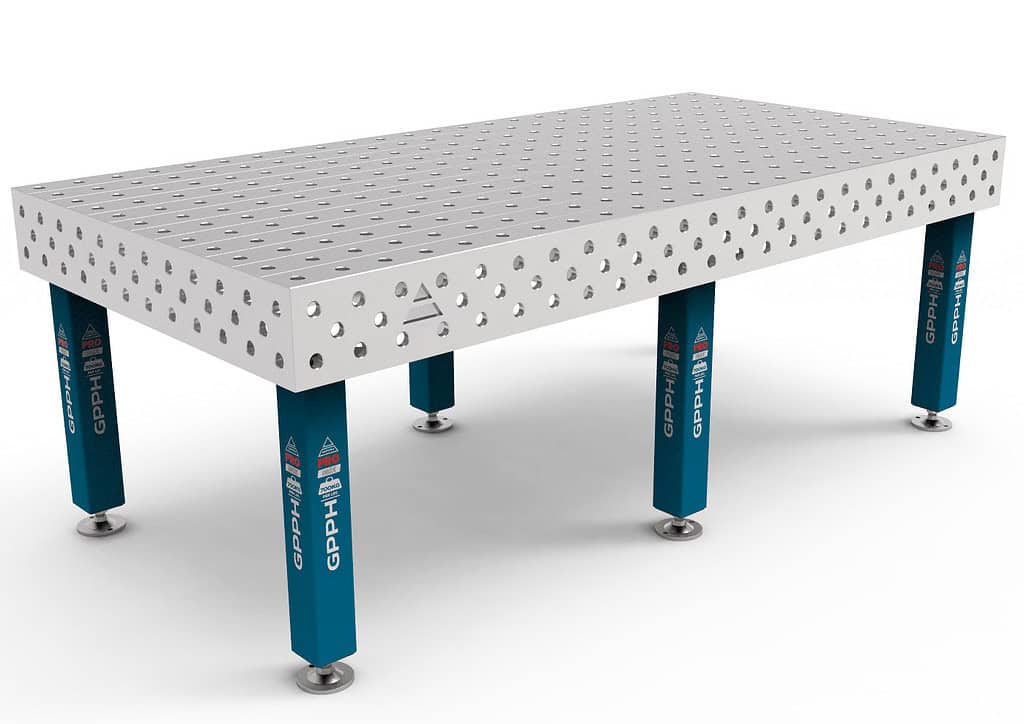
Advantages
- When welding stainless steel components or workpieces, using a stainless steel welding table prevents contamination and ensures integrity of the welds.
- Stainless is much more resistant to rust and corrosion, making it ideal for welding environments with high humidity, exposure to chemicals, or outdoor use.
- If the welding table will be visible to customers, or if the workshop prioritizes a professional and polished look, stainless can provide an upscale aesthetic.
- Certain industries, such as food processing, pharmaceutical, and medical device manufacturing, have strict regulations and standards regarding the materials used in their production facilities. Stainless welding tables may be mandated in these industries to meet the required hygiene and contamination control standards.
- Although stainless steel welding tables are generally more expensive than carbon steel ones, they offer exceptional durability and longevity.
Disadvantages
- The cost of a stainless steel welding table can be prohibitive. It’s often 3 times as much as carbon steel due to the higher material cost and more stringent environmental variables required for manufacturing.
- A slightly lower thermal conductivity compared to carbon steel means stainless tends to hold heat longer than carbon steel, or aluminum surfaces.
- Surfaces can be marred by welding spatter if not protected, which is also true for other materials – but stainless is normally kept extremely clean to prevent contamination and without oils or anti-spatter coatings it’s more susceptible to certain welding processes like MIG.
Aluminum (or AL/CU Alloy)
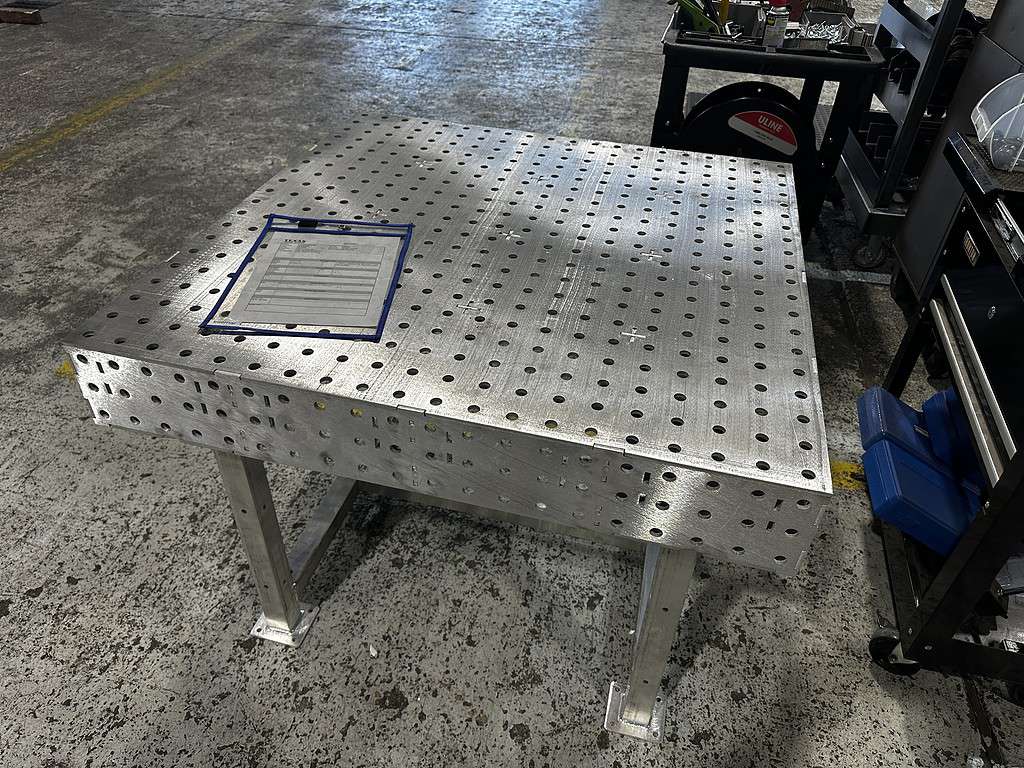
Advantages
- Aluminum is obviously the most lightweight and portable of the common materials.
- It offers excellent corrosion resistance and will never, ever rust.
- It’s non-magnetic, which can be advantageous in certain welding applications.
- Aluminum, being a non-ferrous metal, eliminates the risk of iron contamination when welding stainless steel components. It is generally a much more economical option for shops working exclusively with stainless or aluminum.
- Aluminum has excellent thermal conductivity, which helps dissipate heat during welding and reduces the likelihood of distortion in the workpiece.
Disadvantages
- Aluminum is a much softer material compared to steel, and is prone to scratches and dents from heavy usage.
- Tooling could also potentially put enough pressure on the surface to damage it since whatever is being welded is likely stronger than aluminum.
- It’s non-magnetic, which can be a disadvantage in certain welding applications.
- Aluminum welding tables will always be more expensive than carbon steel.
- For applications where a heavy table offers benefits, aluminum won’t provide the same level of stability.
- Aluminum tables are generally less common, potentially limiting options.
Beware of Mystery Metals!
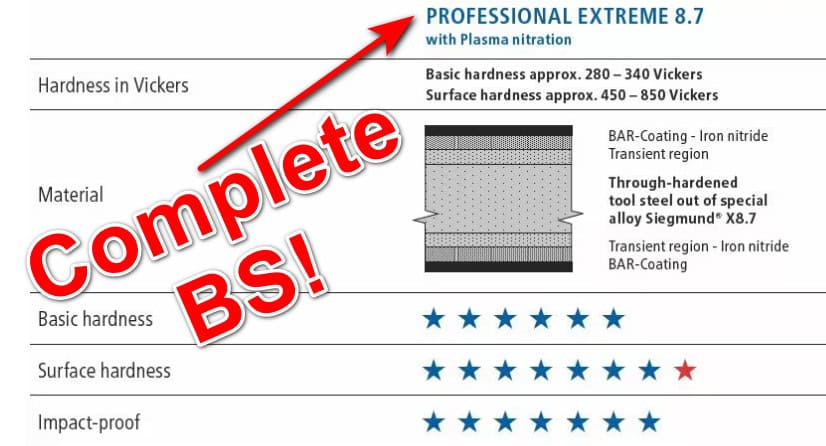
Unless a welding table manufacturer specifically discloses the exact formulation of material they are using, do NOT believe that they have developed some proprietary blend or alloy that has magical characteristics that others don’t. Steel is a literal commodity (see: NYSE American Steel Index), and with the exception of special industries there have been no real innovations in decades. Most of the common construction grades of material have been around for 50+ years if not much, much longer:
- 1018 Steel (Not disclosed, but widely used by Siegmund according to chemical analysis):
- 1018 steel is a low-carbon, mild steel that’s been used for a long time.
- The SAE (Society of Automotive Engineers) standard for grading steels, which includes 1018, was introduced in the 1930s.
- The composition and properties of 1018 steel have been known and utilized since the early 20th century.
- A36 Steel (Disclosed by WeldTables.com as their main material):
- A36 steel is a structural steel specified by the ASTM (American Society for Testing and Materials) standard. It’s a common steel for weld table manufacturing.
- The ASTM A36 standard was first introduced in 1960.
- Prior to the introduction of the A36 standard, similar structural steels were used in construction, but not necessarily designated as A36.
- A572-50 Steel (The primary material we use at Texas Metal Works):
- A572-50 is a high-strength low-alloy (HSLA) structural steel specified by the ASTM standard.
- The ASTM A572 standard, which includes the Grade 50 variant, was first introduced in 1966.
- The development of HSLA steels like A572-50 began in the 1960s to meet the demand for higher strength and better weldability in structural applications.
- Cast Iron (Used by Fireball Tools)
- When companies claim their tables are made from cast iron, they are likely referring to the more modern ductile iron process.
- Cast iron has a long history dating back over 2,500 years. The earliest known cast iron artifacts were found in China, dating back to the 5th century BCE during the Zhou Dynasty.
- Ductile iron, a more advanced form of cast iron with improved mechanical properties, was developed in 1943.
When companies like Siegmund claim to use “proprietary” blends of steel, keep in mind that if they have a foundry just change one of the ingredients by .01%, it’s now “proprietary”. But it’s also hype developed by fancy marketing departments. If they won’t disclose a specific blend, they either have something to hide, or they’re being deceptive – there are no other options.
Most commonly imported tables from countries such as India and China, especially in relation to cast iron, use super cheap materials which are often just blends of whatever scrap they threw into the mix. With other blends of material they often lack quality control capabilities, or simply lie, meaning you can’t rely on it when it matters. And since welding tables need to be durable and hold their flatness forever, it’s far from guaranteed with some import tables. There is also risk of an unknown blend of material breaking and causing injury.
Surface Type
Welding tables are generally produced with a few variations. Traditionally, welders built their own tables using flat plates, however currently welding tables now employ some type of holes for built-in fixturing using tools specifically made for the purpose. (More on that later.) Fixture tables can reduce setup times by utilizing rapid jigs, allowing welders to quickly and easily secure workpieces.
3D vs 2D
2D Welding Tables
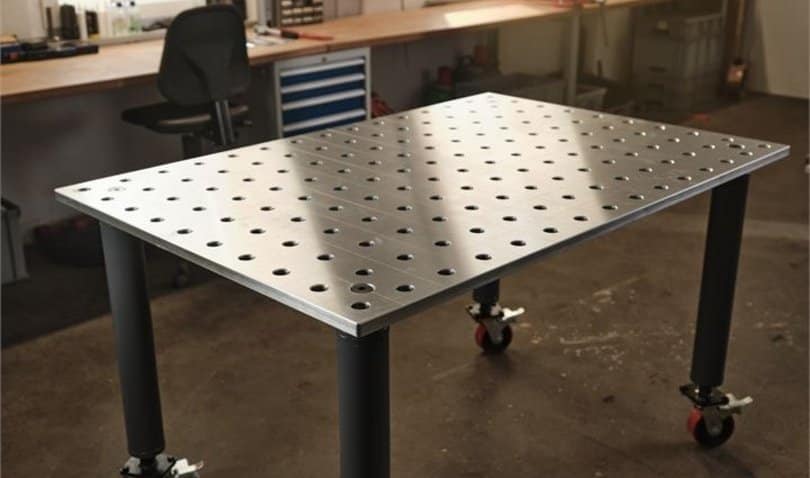
- Have a flat, planar surface without any built-in three-dimensional features.
- They are simpler in design and construction compared to 3D tables.
- The vast majority are simply plate steel, with no / few holes in them.
- Often much more affordable than 3D tables due to their simpler design and construction.
- Suitable for a wide range of general welding projects limited to the size of the table surface.
- These tables can be a simple solid surface, or may incorporate standard sized holes for tooling.
- Very hard to expand since they can’t easily be bolted together to maintain a flat surface.
- Not as flat as other table types because they usually lack support around the edges.
3D Welding Tables
3 Dimensional tables are very easy to spot, but the key takeaway is that these newer generation tables are up to 30 times stronger than 2D table tops.
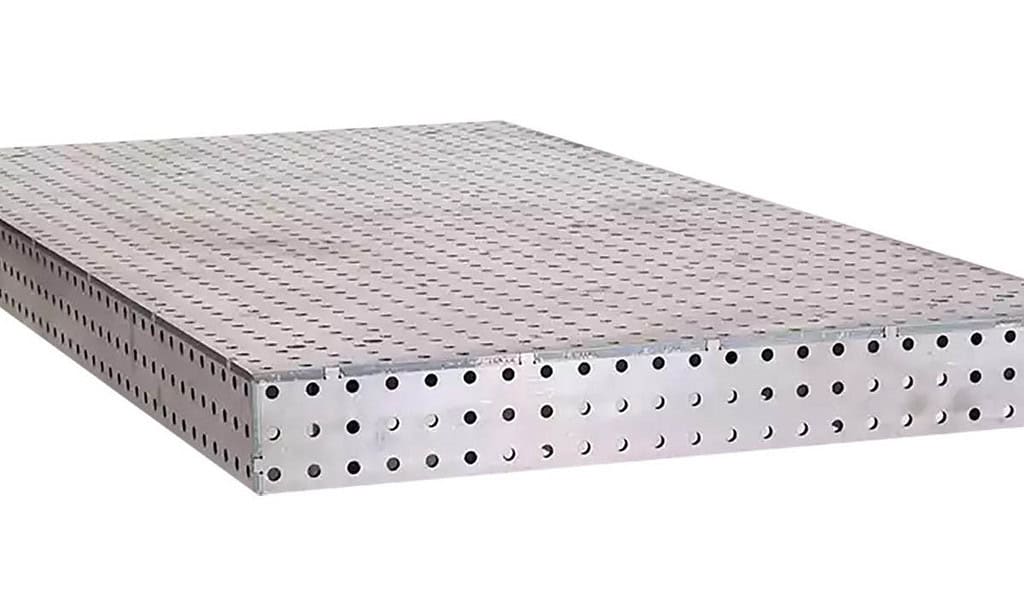
- They have a flat planar surface, plus sidewalls all around that allow for tooling, fixtures and expansion.
- Typically 3D tables are an order of magnitude flatter than 2D welding tables.
- 3D welding tables almost always incorporate built-in features such as slots, holes, or modular fixturing systems that help maintain consistent positioning and alignment of workpieces, resulting in improved accuracy and repeatability.
- Allow for more advanced and precise fixturing of workpieces, enabling welders to work on complex projects.
- 3D welding tables feature modular designs, allowing users to reconfigure the table layout or add accessories to suit specific project requirements.
- For example: vise mounts, extensions, or even other tables can be bolted to the sidewalls.
- Due to their more complex design, 3D welding tables are typically more expensive than 2D tables.
Slats or Rails

- Some welding tables are based on a rigid frame that has been machined to be extremely flat. Modular top sections are then bolted to the frame.
- These tables typically use T-slot tools or traditional C-clamps to hold down material.
- Since these tables are sectional sometimes there can be an advantage by leaving out certain slats to accommodate irregular shaped work pieces.
- They rely on an extremely strong, flat frame combined with extreme consistency in thickness of the slats. This can increase manufacturing complexity.
- Improper installation can dramatically impact table flatness. For example a spec of dirt between the frame and a slat can have a serious impact.
- If a single slot is damaged it can easily be flipped or replaced.
Blocks
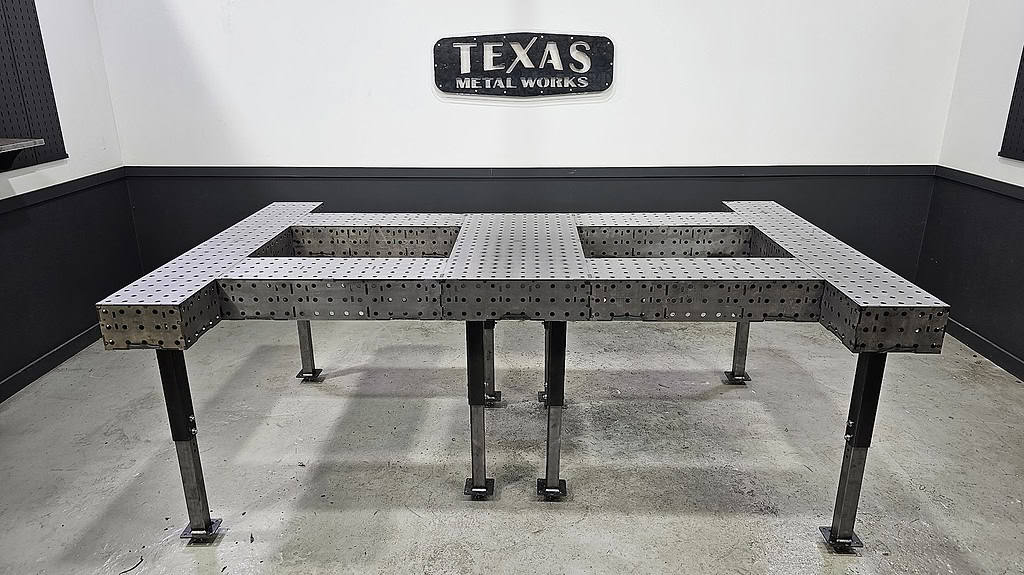
- Welding tables can be assembled by connecting multiple 3D blocks into customizable shapes that work well for specialized manufacturing.
- The blocks are usually just miniature versions of 3D welding tables, and are offered in a variety of sizes.
- Blocks can also be used in conjunction with other welding table types, for example to build vertical fixtures, or to interconnect multiple tables.
Thickness
Material thickness, as it relates to welding tables, is a topic of much contention. Some of it due to a lack of understanding, some due to individual desires or preferences, and some due to actual circumstances or processes. It has been my experience that people generally overestimate their requirements, which is understandable since there is very little information out there to base a decision on.
Table Type
One variable when thinking about thickness is whether we’re looking at a simple flat plate welding surface, or a 3 dimensional table with some sort of support infrastructure. There’s a wide range of designs that can support a tremendous amount of weight, however the trick is to be able to support weight without deflection. Or at least within a range of allowable deflection.
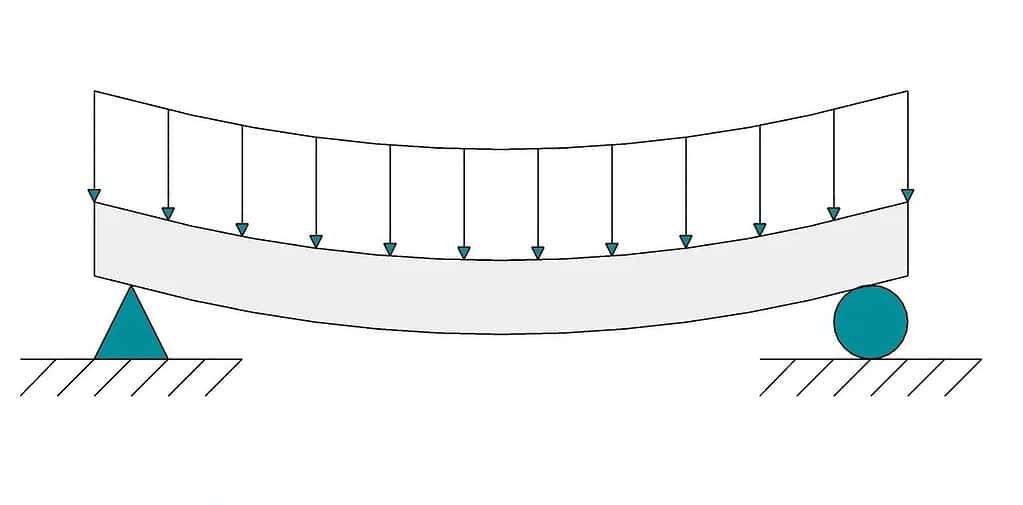
By that I mean If you put a ton of weight on a table and it sags by an inch, you’re not going to be able to build anything flat on that surface. However, if it only sags by 1/64th of an inch, it’s probably within an acceptable range of tolerance for you to build things on it.
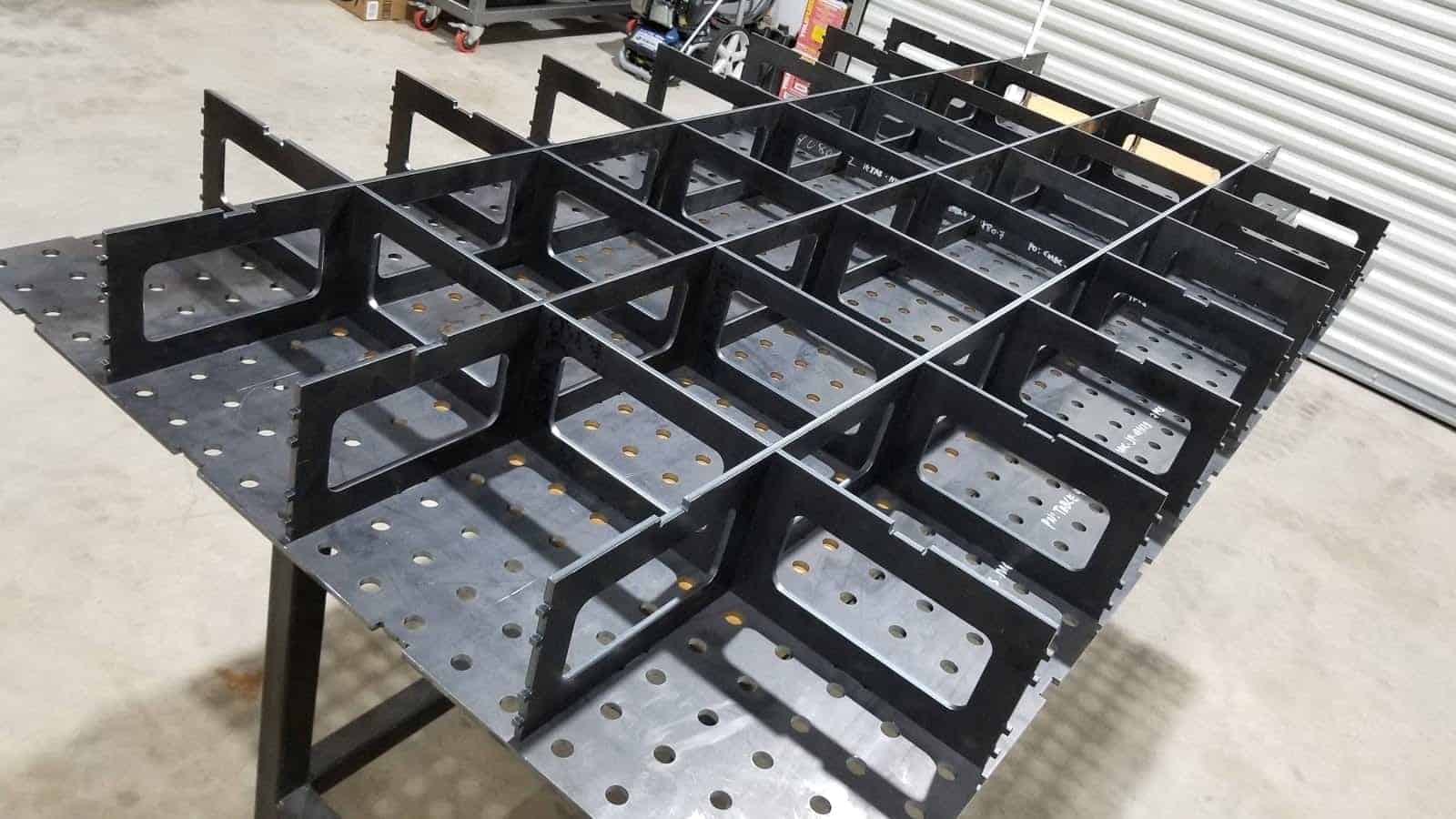
Having said that, if you build a table out of only a flat plate on four legs, the table is going to need a lot more mass to resist the deflection of the weight placed on top of it. Conversely, you could potentially use a fairly thin sheet of material as long as it has a large infrastructure underneath supporting it. this is how the engineered 3D tables Manage to stay so flat under heavy loads even though they have a fairly thin top, like 3/16 of an inch or 1/4 of an inch.
If there are many 6″ or 8″ cris-crossing ribs under the surface it is actually much stronger than even a sheet of much thicker steel.
Material Choice
The type of material the welding table is made of also affects the thickness requirements. For example, as discussed earlier there are some advantages to using cast iron since it can be good at resisting deflection, and will stay very flat after machining. However, since the material is much more brittle than other choices it needs to be much thicker in order to resist breaking.
Breaking isn’t the only concern. Welding tables also need to be tough enough to resist the abuse they are going to be taking. If a welder is tossing heavy material onto the table, or pounding on parts with a hammer, or accidentally drops something heavy on the surface, the material needs to either completely resist the impact, or it needs to spring back. I wrote an article comparing A36 and A572-50 previously and the short version is that a tougher material of any given thickness can spring back from a heavier blow, thus preventing permanent damage to the table.
Workpiece Requirements
Along the same lines, what you are working on also factors into the table thickness required. If you are going to be fabricating things out of small parts and tubing there is almost no way you’re going to damage any surface. But if you’re going to build fire engines on the table you better be prepared for the occasional massive impact from dropping a bumper or something on the surface!
Generally speaking, you can make up for an inferior material with more mass – or you can go with a thinner material if you have medium to light duty projects, the table design has a good support infrastructure, or if your tolerances are fairly low so a bit of deflection isn’t going to hurt anything.
Sizes and Configurations
Welding tables are typically found in sizes ranging from 2′ x 3′ on the smallest end to 5’x10′ on the largest end. There are a few rare instances of larger contiguous tables, however the new 3D style tables are designed to be used in conjunction with one another to create larger or more complex work surfaces. There is truly no limit to how the tables can be assembled.
For example, if a project required some access to the bottom of a complex frame that needed to be fixtured and built on a table, you could use a single solid table, and then smaller table blocks to connect to it .
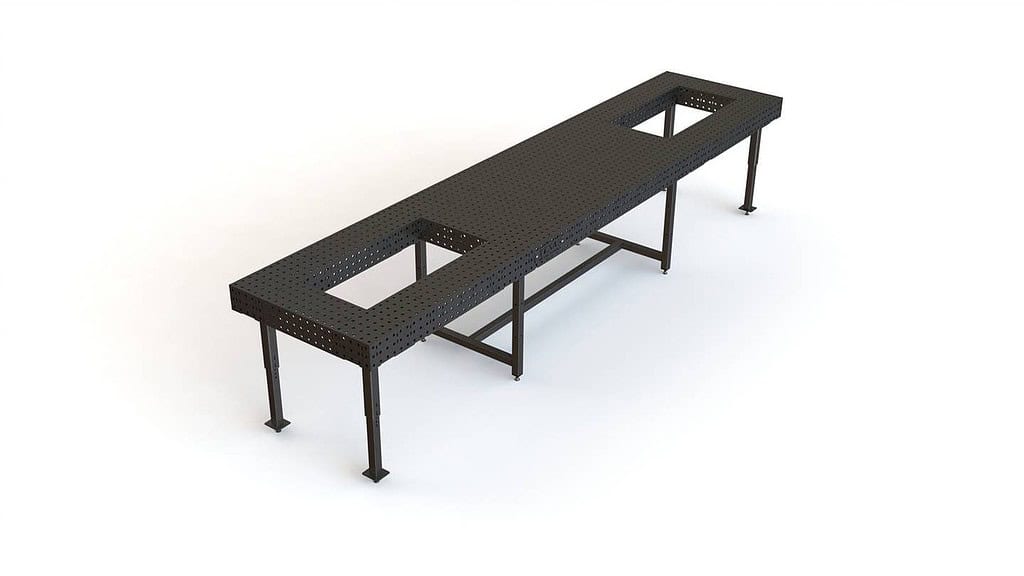
And there is no reason you’d have to stop there. You can continue using the blocks to even build upward from the surface in order to support taller components on the workpiece.
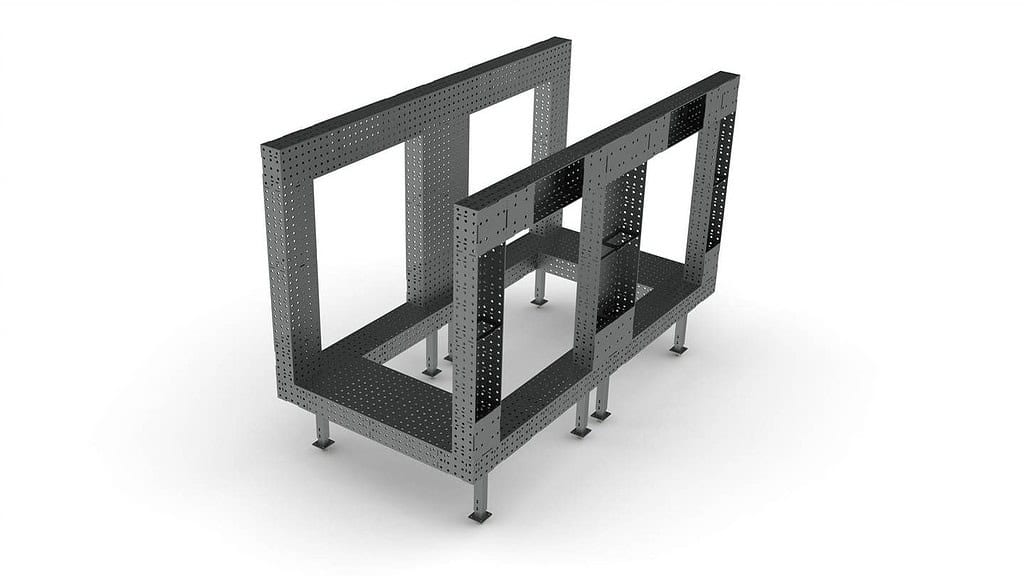
So it’s important to choose the size that’s most useful as a stand-alone work table, but also keep in mind that you aren’t locked into that size in the future since you can add extensions, additional tables, and other modifications to expand capabilities.
Ergonomics
This topic is so important, and so misunderstood, that it probably warranted being the first thing we discuss. But we’ll tackle it now anyway…
There are many ergonomic studies of table top heights which are critically flawed when it comes specifically to fabrication. For example, standard tables for work desks or dining range between 28-30″. While standard kitchen countertops are about 36″. These seem to make sense because you’re sitting at a table, and standing by a countertop. Consequently almost the entire welding table industry has set their standard heights at 36″.
But it’s just not that simple. Because the nature of welding is different than that of just standing and interacting with things on let’s say a countertop – the welder must lean for precision work, and prolonged leaning worsens back strain.
Why a Higher Table Reduces Back Strain
Experiencing less back strain comes down to minimizing how far you have to bend forward, even slightly.
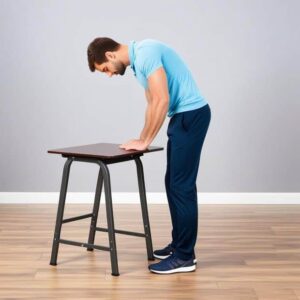
Small Forward Bends Add Up
- When a table is too low (e.g., 36″ for someone 6′ tall), you naturally bend at the waist—even if it’s just a few degrees.
- Over time, even slight bends put tremendous load on your lower back. For example:
- At a 20-degree forward bend, the force on the lumbar spine increases by ~50%.
- At a 30-degree forward bend, this load can double.
Arm and Reach Trade-off
- A higher table brings the work closer to your natural standing posture, where your arms can work comfortably at or slightly below elbow height.
- It prevents you from “hanging” your torso over the table to reach, which engages your back muscles unnecessarily.
Stronger Posture = Lower Back Relief
- A table height closer to your elbows (or just below) allows you to maintain a neutral spine without leaning or rounding your back.
- When the table is lower, the tilt in your torso—small though it may be—activates the erector spinae muscles, which fatigue quickly when unsupported.
Optimal Welding Table Heights
I believe the ergonomic sweet spot is about 2″- 4″ below elbow height, which is adjusted upward from standard counter heights based on the welder’s tendency to lean.
Welder’s Height | Optimal Table Height |
---|---|
5’2″ – 5’4″ | 34″ – 36″ |
5’5″ – 5’8″ | 36″ – 38″ |
5’9″ – 6’0″ | 38″ – 40″ |
6’1″ – 6’4″ | 40″ – 42″ |
Over 6’4″ | 42″ – 44″ |
If the table needs to accommodate welders of varying heights, adjustable-height tables or risers are the best solutions.
Reference Data
Rigorous studies have quantified the load increase on the lumbar spine under forward bending:
- Nachemson’s Study on Lumbar Disc Pressure:
- At 20 degrees forward flexion, lumbar disc pressure increases by ~50%.
- At 30 degrees, the pressure doubles relative to standing upright.
(Source: Nachemson, A. (1965). “The load on lumbar discs in different positions of the body.” Clinical Orthopaedics and Related Research.)
- Why Load Increases:
- When the spine bends forward, the muscles of the lower back (erector spinae) must work harder to counterbalance the forward shift in weight.
- This increased muscle activity combined with torque amplifies the load on the spine.
- Practical Example:
- According to WorkSafe BC and OSHA ergonomic guidelines, bending the trunk forward by 20-30 degrees without proper posture or table height can exert 1.5–2x the load on the lumbar spine compared to standing upright.
Mobility
We’ve talked about a lot of different considerations so far, but mobility is another factor when choosing a welding table. Choosing between leveling feet, casters, or both depends on your workflow, shop setup, and the types of projects you tackle.
Leveling Feet: Stability First
Leveling feet are special feet that thread into the bottom of table legs that allow you to level your table on uneven floors. The concept is that when a table is placed on the floor and it is wobbly, you manually adjust the length of the leveling foot down until it is making contact with the floor. This stabilizes the table and also gives it the full weight bearing capability.
Leveling a table is also essential to remove any sort of a twist, and to improve flatness.
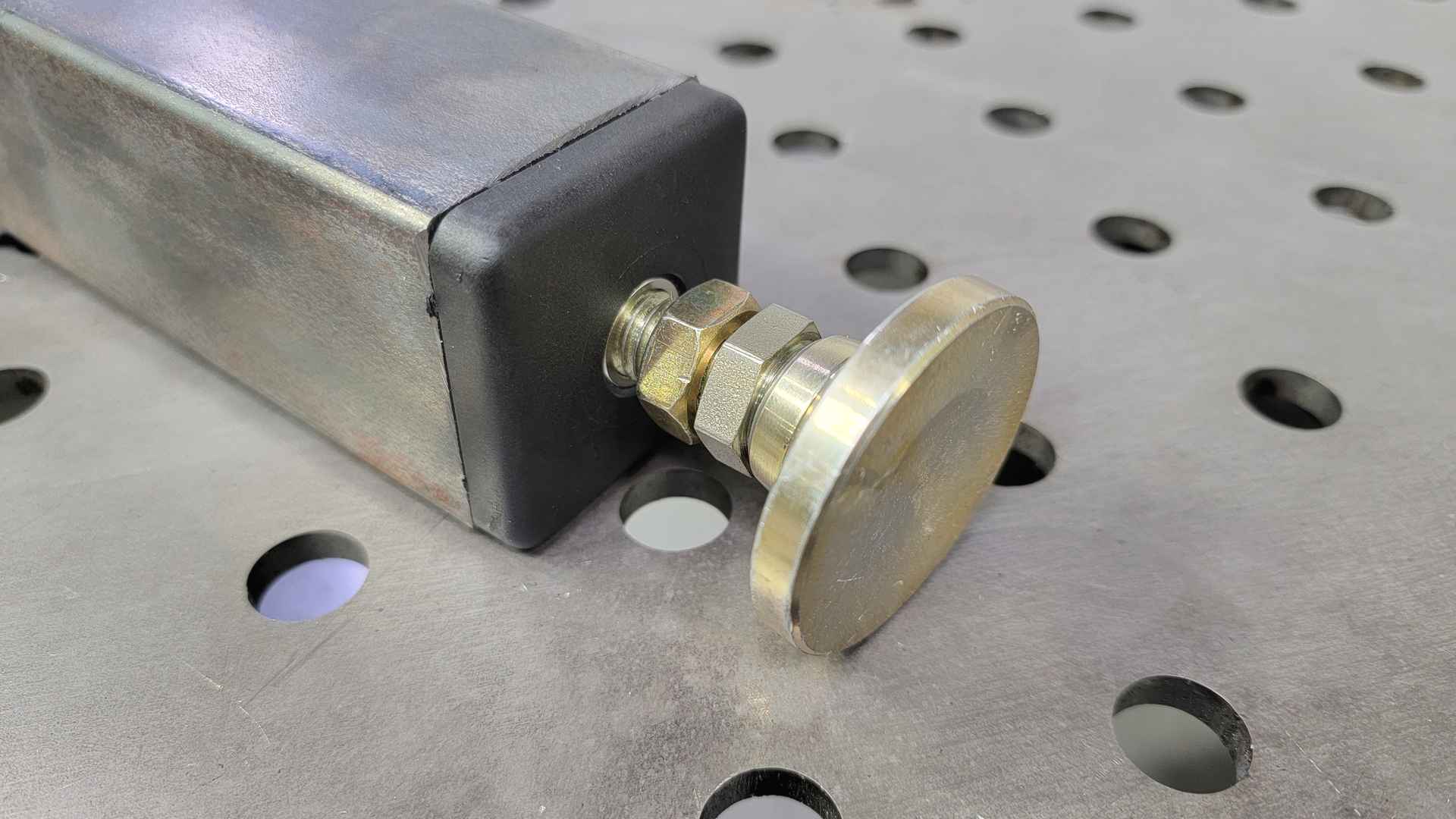
When to Use Leveling Feet:
- Precision Work: Stability is king. Leveling feet eliminate movement and vibration, ensuring accurate welds.
- Uneven Floors: Adjustable height compensates for floor imperfections.
- Heavy Loads: Ideal for fixed, heavy-duty tables where weight and stability are priorities.
Casters: Mobility First
Of course, casters are wheels attached to the bottom of the table legs, allowing it to roll. Every different manufacturer has different casters, and this is an entire discussion on it’s own! I am very partial to the ones we offer, which are “total lock” style – meaning they will neither roll, or swivel when locked.

When to Use Casters:
- Small Shops: Flexibility to move the table when space is tight.
- Multi-Use Workspaces: Tables can be moved out of the way for other tasks.
- Temporary or Mobile Welding: Rolling tables make it easier to move between work areas or outside.
Both Options: The Best of Both Worlds
A combination setup with casters and leveling feet – typically retractable casters that raise or lower to engage wheels or stabilize the table.
When to Use Both:
- Heavy Tables That Need Occasional Mobility: Move the table when needed, then stabilize it for work.
- Precision and Flexibility: Achieve rock-solid stability when working and mobility when rearranging the shop.
- Large or Dynamic Shops: Tables that need to move between stations or processes.
Fixturing
There are far, far too many tools available for welding tables to tackle that here, however we should touch on the different categories of tooling that are available.
The Two Main Systems: 16mm vs. 28mm
There are two main systems of standardized tooling on the market. The tooling is basically identical, but different sizes.
Feature | 16mm System | 28mm System |
---|---|---|
Hole Diameter | 16mm | 28mm |
Table Thickness | Typically 1/4″–3/8″ (6-10mm) | 1/2″–1″ (12-25mm) |
Use Case | Light to medium-duty work | Heavy-duty work, larger setups |
Precision | High precision, tight tolerances | High precision, heavy-duty |
Weight | Lighter overall system | Heavier and more robust |
Tooling Size | Smaller clamps and stops | Larger, heavier tooling |
If you purchase a welding table with round holes, as long as they claim to support either 16 or 28mm tooling you should be able to purchase the tools from different manufacturers and mix and match with the table you buy. ANY other size is non-standard.
Some companies do offer different sized tooling. For example Fireball Tools utilizes 3/4″ tooling, but since they are the only manufacturer using this size it will limit the range of compatible accessories to a single tooling manufacturer.
Slotted Tables
Slotted welding table designs often include 16mm tooling holes, but since they have gaps between the slots it’s also possible to use different tooling such as T-slot clamps. Those clamps are generally made for woodworking tables, so are hard to find. But, some common types include:
- Hold-down clamps: Press materials firmly against the table.
- Toggle clamps: Quick-action clamps for speed and repeatability.
- Vertical and horizontal clamps: For precise holding of workpieces at angles.
- Quick-thread T-slot bolts.
- Studs with nuts for multi-point fixturing.
Other Tooling
Magnetic squares, clamps, and stops are also popular for quick adjustments without the need for mechanical fastening, assuming you aren’t using a stainless or aluminum table.
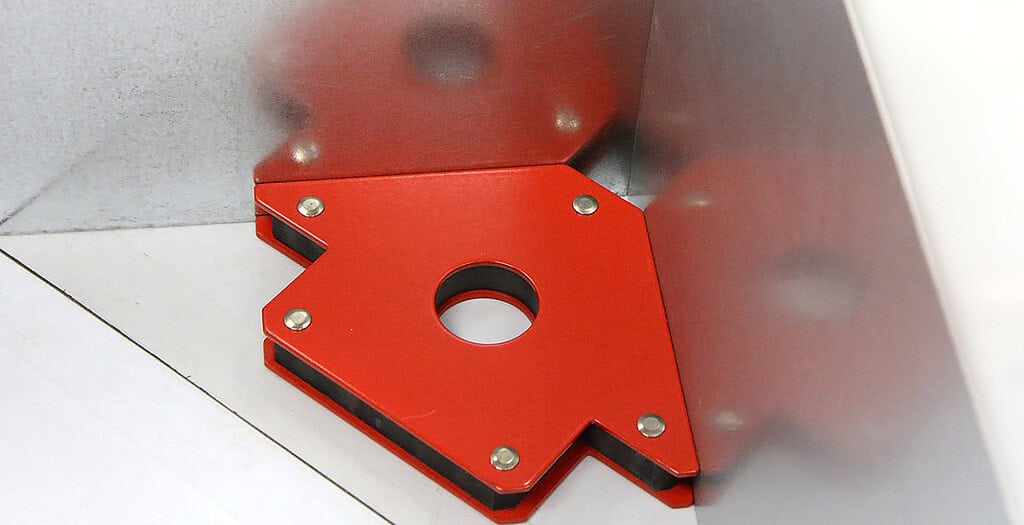
And of course any tool that could be used with an old fashioned flat steel plate welding table will also be useful with the tables we’ve been discussing here.
Care and Techniques
Several welding table manufacturers offer tables which have some sort of surface treatment such as plasma nitriding, or other hardening / coloring processes. They ALL claim these treatments will prevent rust, spatter and damage.
The Claims Are Exaggerated!
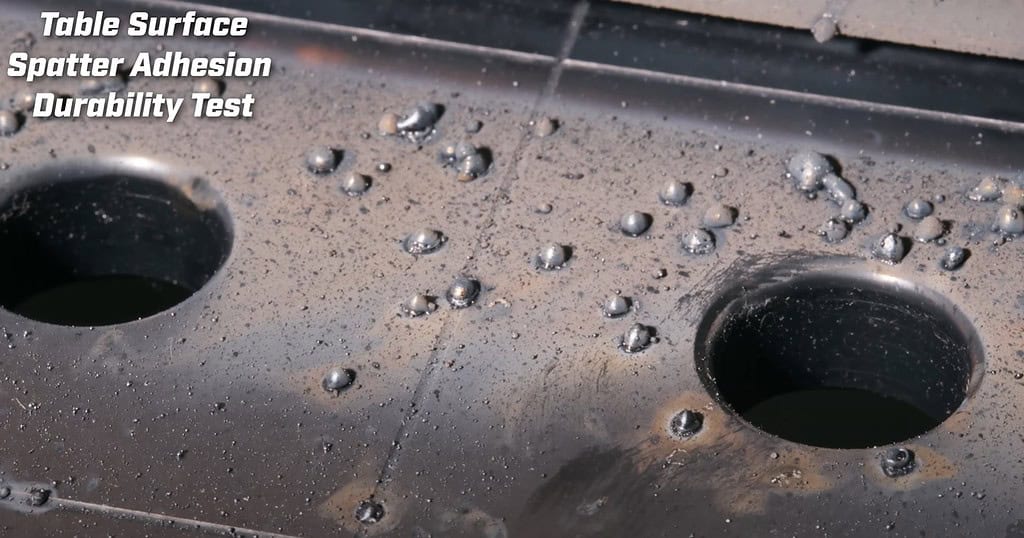
A surface treatment will help protect the table and provide some rust protection and some will provide very, very shallow surface hardening (like .002″). But we have experienced that simply laying a piece of wet plywood on a nitrided surface will rust it within 1 hour and permanently damage the surface.
- Welding spatter will also absolutely stick to ANY coated welding table surface, though a coating will help minimize it.
- Scratches can and absolutely will occur regardless of surface treatment.
So, coating = good. But it ain’t going to keep a table pristine over time. They will still need the same care as a non coated table if you want them to work like new for a long time.
Use of Anti-Spatter Agents
Regardless of the table material, the use of anti-spatter sprays or gels can significantly reduce spatter adherence. These agents form a protective barrier on the table’s surface, making it easier to clean and maintain.
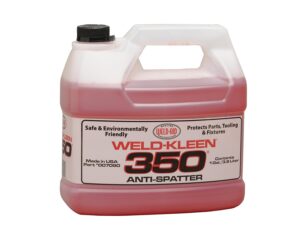
We also have an entire article about caring for the surface of a welding table here.
Elevating The Work Product
Another method of protecting the surface, while also providing some other benefits, is to use precision machined blocks under the work piece to elevate it above the table.
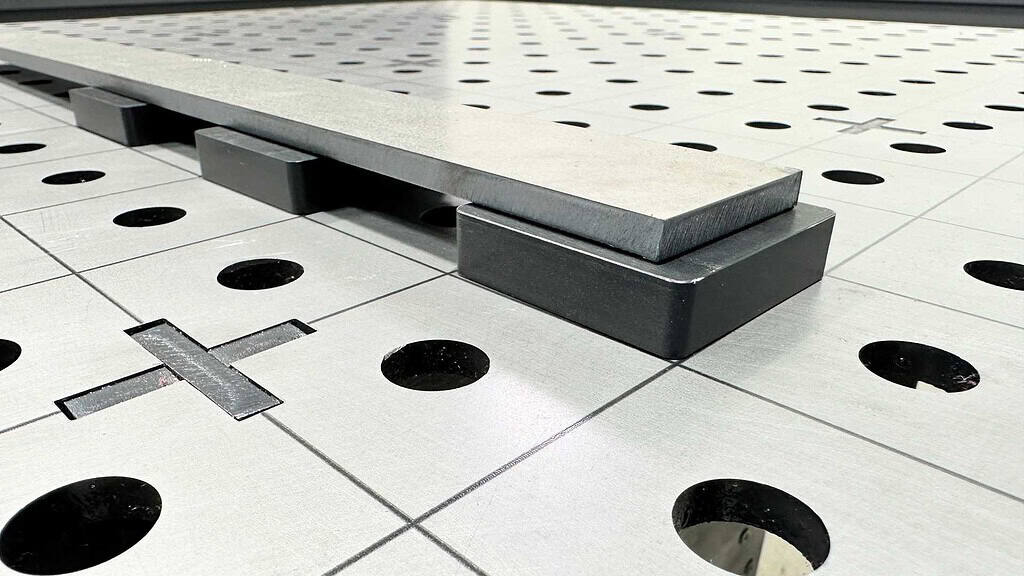
If you are using a messy weld process such as MIG or flux core, the closer the BB’s are to the surface, the hotter they are when they make contact. By elevating the work it allows critical air cooling which helps keep things from sticking.
In fact, using this process combined with anti-spatter will prevent almost all BB’s from sticking, while also protecting the surface from rust.
In Summary
We’ve covered a lot of ground here, and there are many more variables than most people would expect. So it’s Ok if you’re feeling a little overwhelmed. Frankly, I’m shocked if you actually got to the end of this! Maybe drop a comment below if you actually read it. 🙂
You can also drop a comment if you see an error or omission, feel like there was some bias, or just have other questions! Because if you’re left wondering something I guarantee other people are too. So let’s make sure we cover all the bases.
And as always, reach out if you need help with anything. We’re always at your service…
2 comments
K-dubya
I’m a total newbie learning to weld for my retirement years on the farm. As I was shopping for a welding table, I happened across your blog … and I needed to go no further!
All my questions have been answered and your tips/tricks/advice absorbed.
Thanks for the time you devoted to the blog!
John P.
Thanks for the positive encouragement. Happy to have helped!!!