At Texas Metal Works we own a very expensive and extremely accurate laser measuring system. It’s the same system used in the aerospace industry, and we use it to test our tables for quality control purposes. Since most people don’t have access to a $100,000 measuring tool, I wanted to share some information that you’ll never normally run across. Although the example I’m going to go over here is one of our own welding tables, the principals apply to EVERY table made.
Background Info
We used one of our 70″x140″ welding tables in this example. Not only is it the biggest contiguous welding table we build, but one of the biggest anyone builds anywhere. Generally speaking, the larger the table, the more difficult it is to keep things absolutely flat.
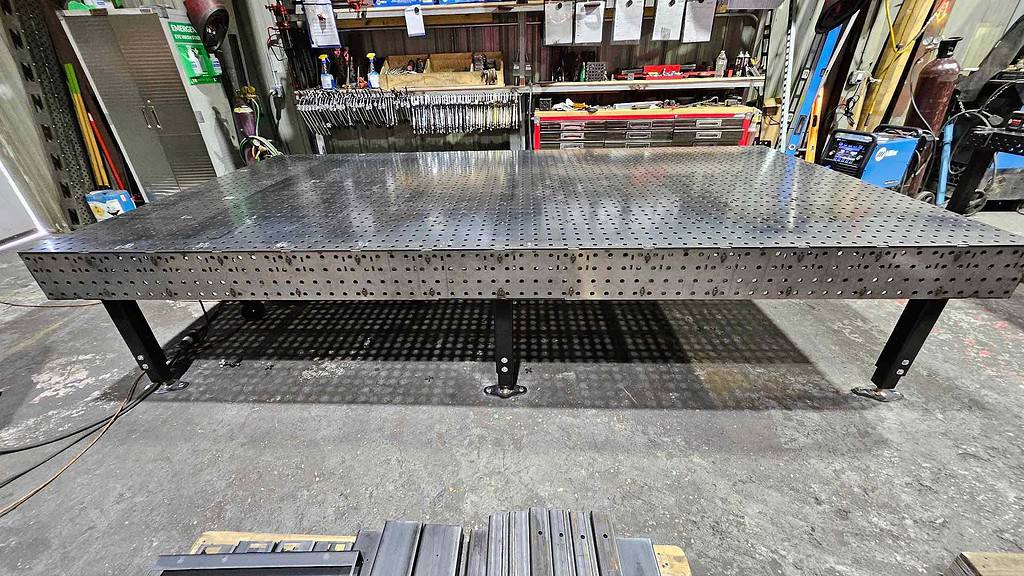
When you purchase a welding table it will generally have one of three different leg configurations:
- Legs with leveling feet
- Legs with casters
- Legs with casters and leveling feet
The heavy duty tables we build all have either 6″ or 8″ ribs and sidewalls to provide strength and torsional rigidity. Generally speaking, even when these tables are rolling around on casters they aren’t really impacted by the flatness of the floor they’re on. You can see this in action when you roll over a low or high section of floor and one of the casters comes off the ground.
Even with projects weighing a few hundred pounds, the table should maintain relative flatness when it’s on casters. However, if you start putting 1,000 pounds or more on the table you could see some flexing. Well, I should say, you could probably measure some flexing even though it might not be noticeable to the human eye. So when you’re dealing with heavy projects it’s always recommended to use leveling feet, and to take the time to try and correct for the lack of flatness in the floor.
If you want to be REALLY precise, we advise one more step. If you look closely at the photo of our table you’ll see that the leveling feet are sitting on steel plates which are bolted to the floor. In fact, the welding foot has been tack welded to the steel plate!
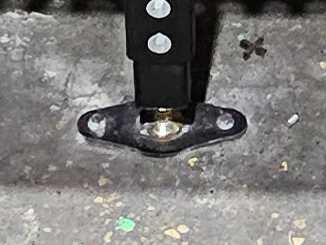
We do this because once the table is leveled it’s specific to that one position on the floor and if the table were to move, it would no longer be level.
Initial Measurement
After installing this table we took a 96 inch level and manually adjusted each of the feet while moving the level around the table and continually testing for flatness. The easiest way to do this is to put the level on the surface and stand back with your eyes right about surface level looking for light shining between the level and the surface. You can also use a feeler gauge if you want to measure the gap. Keep in mind that these relatively inexpensive levels are not perfectly flat themselves! But it’s better than nothing.
Anyway, after we leveled the table in this manner we measured the flatness with our laser measuring system. Here are the results. (Detailed report here.)
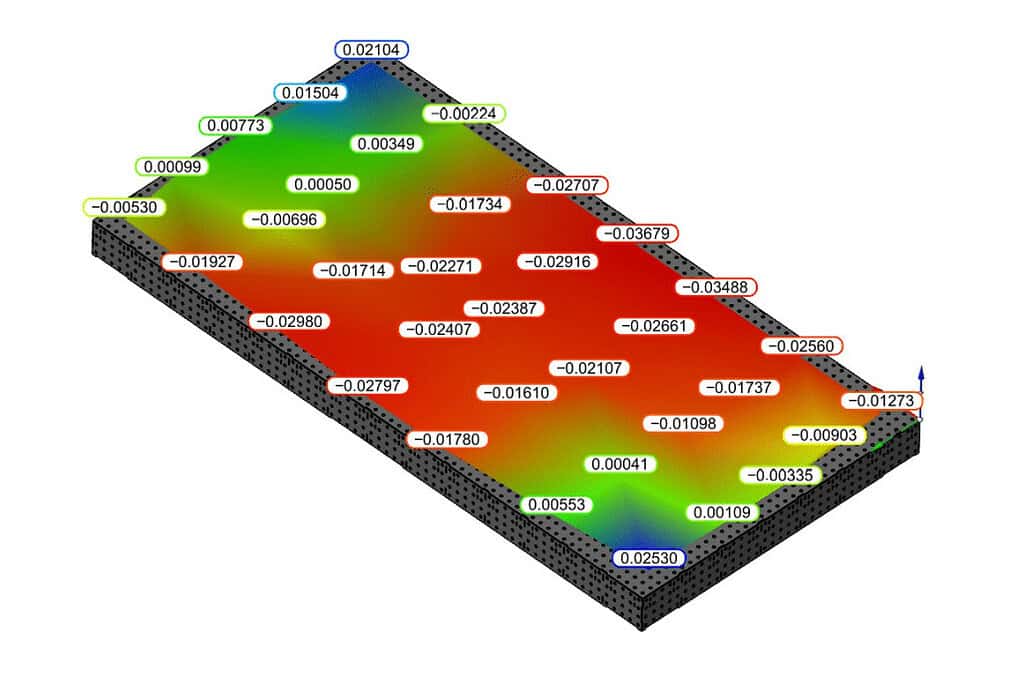
Now, the colors in this report are extremally exaggerated. the worst position is off by .03679″, which is about 1/27″. Not bad for a nearly 6’x12′ table that was leveled by eye.
Post Leveling Measurement
Once we had the initial measurement, we used our laser to adjust each of the 6 leveling feet individually to get them as close to .0000 as possible. We went around the table a couple of times making adjustments because when one leg was zeroed out it would move the others a bit. After about 5 minutes, these are the results. (Detailed results here.)
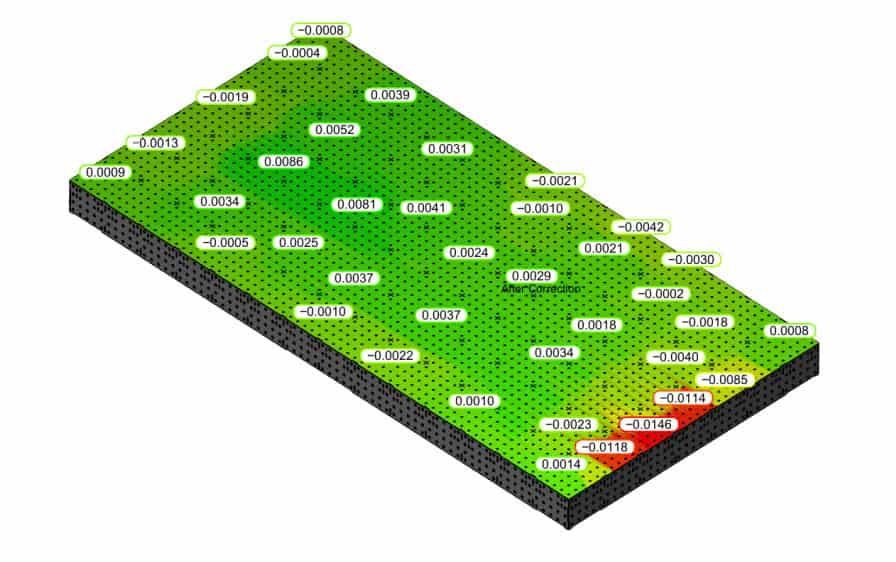
As you can see, there is an appreciable improvement in flatness across the entire surface. We can also see in this map that the middle of one end of the table takes a dip. It looks alarming because it’s in red, but the area is actually only about 1/80th of an inch low.
Here’s the side by side for easier comparison.
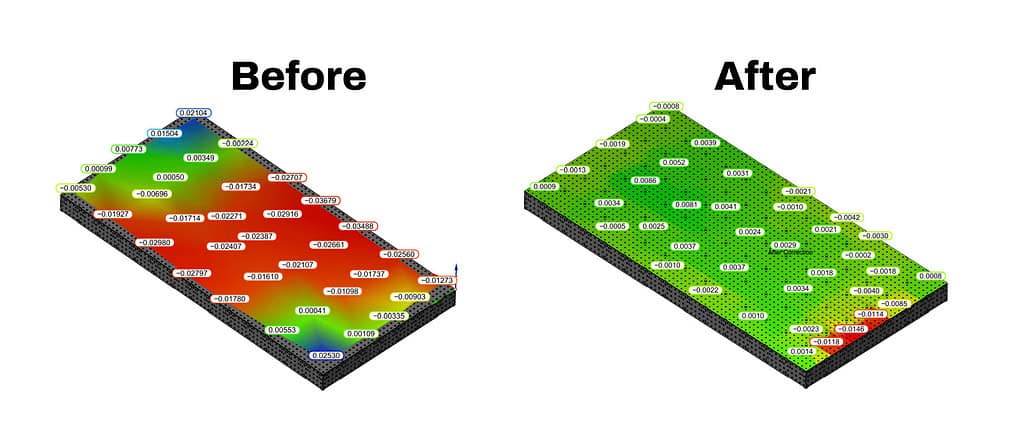
What’s An Acceptable Tolerance?
Flatness tolerances vary significantly depending on the project, customer, material and even process. But one thing that doesn’t change is the fact that generally you can’t build anything flatter than the table you build it on.
Workpieces that are produced by metal removal or are formed from sheet metal can fall under the ISO standard 2768-1:1989. This standard has the following general tolerances for either straightness or flatness. The tolerance is dependent on length in mm.
General Tolerances on Straightness and Flatness | ||||||
Tolerance Class | up to 10 | over 10 up to 30 | over 30 up to 100 | over 100 up to 300 | over 300 up to 1000 | over 1000 up to 3000 |
H (fine) | 0.02 | 0.05 | 0.1 | 0.2 | 0.3 | 0.4 (.016in) |
K (medium) | 0.05 | 0.1 | 0.2 | 0.4 | 0.6 | 0.8 (.031in) |
L (course) | 0.1 | 0.2 | 0.4 | 0.8 | 1.2 | 1.6 (.063in) |
For the ISO standard between 1,000-3,000mm (39.37in – 118.11in), flatness tolerance would range between a very tight .4mm (.016in) to 1.6mm (.063in). So, for example in the case of our table above, even though it’s over 3,000mm long let’s compare to the last column.
- Prior to leveling, the table would not meet either the fine or medium ISO tolerance standards. Therefore if a client wanted you to build a product to those standards on the table it would be unadvisable. (There are creative ways to account for the deviance, but it would be tricky.)
- After leveling, the table would be able to meet all of the tolerances, even by much smaller table standards.
In Summary
You may very well be able to leave a welding table on casters, or just throw it on the floor somewhere without ever encountering an issue with the projects you’re building on it! MOST projects will work just fine with tolerances of 1/16″-1/8″ or more. But for those occasions when you really need to focus on extreme precision, at a minimum we would recommend setting the table on feet and spending a little time manually leveling it out as best you can.
When you need to be absolutely certain you’ve squeezed every bit of precision out of your table, you’ll need to get your hands on a precise measurement system or, more likely, hire a professional who has the tools and training to tweak and certify the flatness of your installation. For the record, the system we employ is from Verisurf.