Comparing the Two Forms of Structural Steel
If you’re trying to understand the difference between steel plate offerings let me see if I can shed some light on the subject. We’ll specifically focus on this topic as it relates to the fabrication of welding tables, however the information and our observations should generally apply to other uses of these materials including shipbuilding, skyscraper construction, truck frames, and everything else.
What Are We Looking For
When trying to determine what the best material is to build a fabrication table, we have to think through the characteristics we’re looking to achieve:
- We want the welding table to be strong. And when we use the word strong, what we mean is we want it to be able to hold a lot of weight without tearing or breaking. The design of the table can dramatically affect strength, but no design could make a balsa wood table strong, so material counts too. We can measure this characteristic in terms of tensile strength, which is the point at which a material fractures (breaks or tears).
- We want the weld table to be tough. A material can be very strong, however have poor impact resistance. For example, a huge block of glass would be able to withstand a lot of weight placed on it. However, hitting it with a diamond tipped tool might shatter it. We need to be able to really beat on the table, and have it withstand a lot of abuse without deformation. We can measure toughness in tables in terms of yield strength, which is the maximum stress that can be applied before permanent shape change occurs. Another measure of this characteristic is resilience.
- We want the table to be as inexpensive as possible. As we’ll see below, since the chemical composition of the two materials is almost identical, the price is similar. However some material differences including the cost of manufacturing does make A572-50 slightly more expensive than A36.
- We want the table to be climate friendly. Steel is, in general, one of the worst polluting materials humans make – at least in terms of CO2 emissions. So if all other things are equal, we should probably prefer the material that generates the smallest footprint.
Chemical Composition Comparison
We need to first examine the exact chemical makeup of the two steel variants to understand what imparts their mechanical characteristics.
Item | C | Mn | P | S | Si | Cu |
A572 Gr 50 | ≦0.26 | ≦1.65 | ≦0.040 | ≦0.050 | ≦0.40 | – |
A36 | ≦0.26 | – | ≦0.040 | ≦0.050 | ≦0.40 | ≧0.20 |
- Carbon (C) in both material types is below .26% meaning they are classified as low carbon steels. Low-carbon steel contains less than 0.30% carbon. Medium-carbon between 0.30% to 0.60%. And high-carbon has greater than 0.60%. As the carbon content increases it becomes stronger and harder. It also becomes less ductile (more brittle). Neither has an advantage over the other, and the fact they are low carbon will contribute to overall toughness.
- Manganese (Mn) is an element that, removes oxygen and sulfur when iron ore (an iron and oxygen compound) is converted into iron. It also is an essential alloy that helps convert iron into steel. As an alloy it decreases the brittleness of steel and imparts strength. It also adds some corrosion protection. Given that A572-50 has this added element, it would be a clue that this grade of steel should be a little tougher.
- Copper (Cu) when added to steel increases corrosion resistance slightly as well as allows for a small bit of hardening.
Mechanical Comparison
Sometimes it’s tricky to compare materials because different references quote different specs. However I’ve done my best to compile the following list. Most of the information comes from here, and I cross-checked multiple other sources to make sure it’s reasonably accurate.
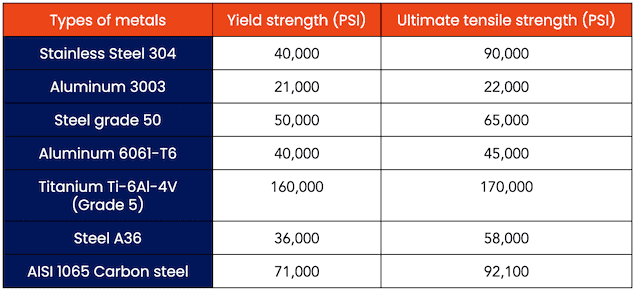
Comparison of A572-50 to A36
Property | A572-50 | A36 | Difference |
Yield Strength | 390MPa | 290MPa | +34.5% |
Fatigue Strength | 280MPa | 200MPa | +40% |
Tensile Strength | 500MPa | 480MPa | +4% |
Resilience: Unit | 410 MJ/m3 | 220 MJ/m3 | +86% |
Resilience: Ultimate | 100 MJ/m3 | 92 MJ/m3 | +8.7% |
Brinell Hardness | 150 | 140 | +7% |
Electrical Conductivity | 7.2 | 12 | -66% |
Observations
- The yield strength improves by about 1/3. This means an impact that would create a permanent dent in A36 would require 33% more energy to dent A572-50. That represents added protection if someone was hammering on a table, or if something heavy were dropped on the surface.
- With a 40% greater fatigue strength, A572-50 could withstand far more abuse in one particular area. So repeated impacts in one spot would more easily cause damage with A36 than A572-50.
- Tensile strength is only slightly improves on A572-50 vs A36, so both materials would ultimately break at about the same time.
- The resilience calculation is a whopping 85% higher with A572-50. Essentially, all the other improvements cumulatively add up to the ability of A572-50 to simply spring back when practically double the force is applied to the surface.
- The measurable Brinell hardness of both steels is pretty close, and relatively low as compared to let’s say a hardened knife which might measure 650 on the Brinell scale. So a knife blade would be stronger and harder to leave a mark on – but it’s also brittle enough to snap in half where A36 or A572-50 would just bend (and often spring right back).
- Interestingly, the A36 steel is slightly more electrically conductive. I would wager a guess that this is due to the inclusion of copper in the materials mix. The conductivity test considers copper a 100, so they are both still way less conductive, but perhaps slightly more power is transferred while welding on A36 than A572-50.
Environmental Considerations
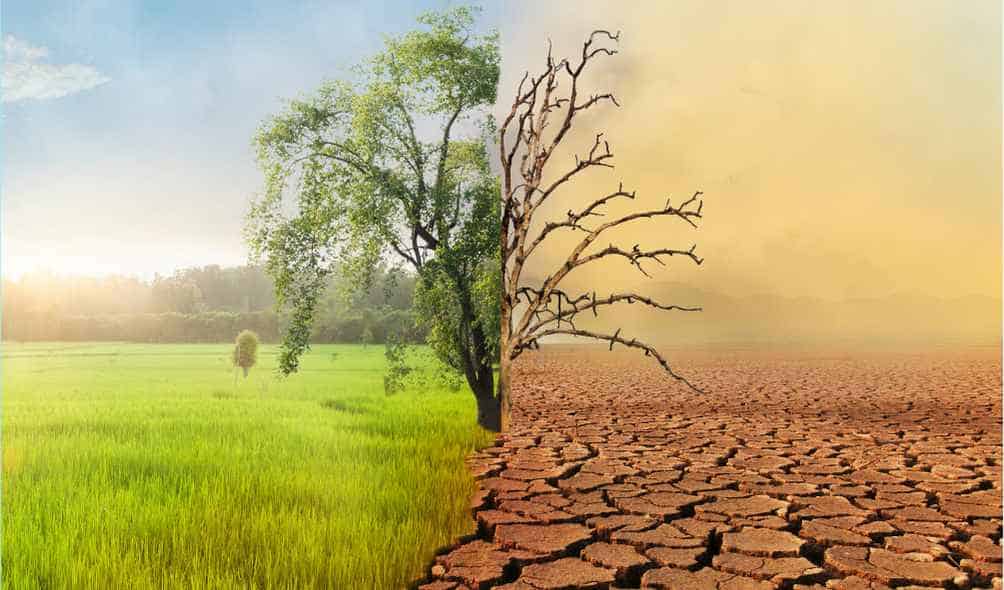
As previously mentioned, if the process of manufacturing one of the two types of steel was significantly more climate friendly, it would behoove us all to use that material – all other things being equal. Here are the relevant stats:
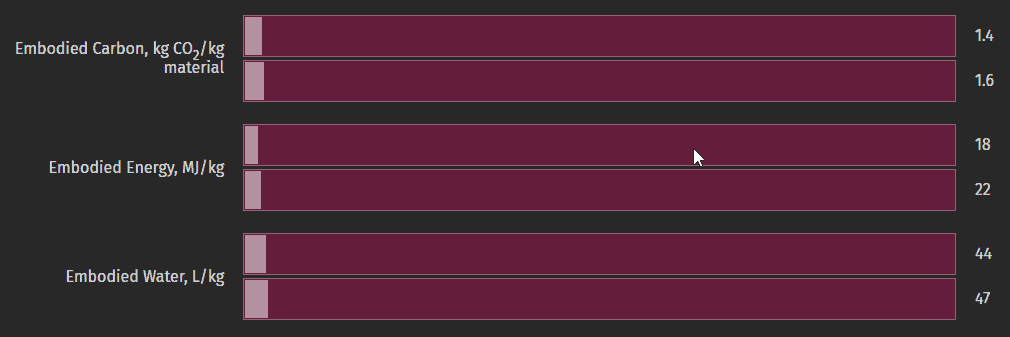
Embodied carbon essentially refers to the amount of CO2 released into the atmosphere as the result of the material creation, while embodied energy shows us the relative amount of energy consumed in production. In both cases we see that A572-50 is a little worse than A36, consuming more energy and polluting a little more. Embodied water, as you might guess, measures the relative amount of water used during the manufacture of the material, and again A36 wins most likely because more energy used requires additional water to go along with it.
Cost Comparison of A36 VS. A572-50
As you might guess from all of the information above, given the additional resource requirements for production of A572-50, in a normal market it’s a slightly more expensive material. Steel is generally sold by the pound, and we’ve seen an average of around 10% premium associated with the cost of A572-50 as compared to A36. At times when the market is under strain that cost difference can swell to 25% or more.
Since A36 is the most commonly produced structural steel, it’s also usually the most widely available. This means it’s also less likely to be running short, even in smaller markets, so the cost is always more attractive.
Conclusions
I know this is a lot of mind-numbing detail, and sorry I can’t make it any sexier! But if you asked me for my interpretation of all this data, here are my takeaways:
- Although it’s more expensive, A572-50 is significantly tougher and more resistant to denting and repetitive beatings. That being the case, if an application is going to call for a lot of really aggressive treatment of a welding table it makes sense to get the tougher material because it will simply last longer. By the way, there are higher grades of A572 that get increasingly stronger and tougher. Of course due to availability they are also increasingly more expensive. So for unique applications that require extreme performance higher grades could be specified.
- Under normal fabrication circumstances A36 is still a VERY strong and tough steel. They build bridges, boats and skyscrapers out of it, so for the vast majority of fab shops a welding table made from A36 would still last a lifetime. Additionally, there’s the bonus that the material is slightly better for the environment and every little bit counts. There’s no reason to waste money and resources if the application is never going to call for the difference in material performance.
- If you’re looking for bragging rights, money is no object, and you want the craziest material available to build a welding table, what you want is AR500. That stuff is 5 times as tough as A572-50, and so is the price. But if you need to make sure your welding table can withstand a .50cal bullet that’s the stuff to get. 😉
I hope this helped clarify things a little bit but as always feel free to reach out if you have other questions or if there’s anything we can help you with!