Welding Table Overview Video
Welding Table Description
Texas Metal Works offers fully fabricated tables shipped FREE – saving you time, hassle, and money! Between the 50″ x 100″ and 60″ x 120″ sits our 60″ x 100″ welding table. When it comes to having plenty of room for multiple stations, or just accommodating large products, it can’t be beat.
The surface is a true 60″ wide and 100″ long, and the 8″ sidewalls allow for additional fixturing outside of the table dimensions. For even MORE room, you can always add one or more of our welding table extensions.
Table Top Features
- A full 60-inch wide x 100-inch long work surface with 8-inch sidewalls.
- Available in 1/4″, 3/8″ and 1/2″ (A572-50) thickness table tops with 1/4″ sidewalls and rib structure
- Standard 38″ surface height (Check out Custom Height – Cut To Order).
- Accommodates 5 foot x 9 foot materials with plenty of room to spare!
- Almost 2,100 precision CNC cut holes (5/8″ / 16mm).
- Accommodates Stronghand and similar tooling.
- Professionally assembled and guaranteed forever!
Table Base Features
- 2″ x 11 gauge heavy tubular steel legs with 2″ x 16 gauge tubular steel cross bracing.
- Optional Casters: 8″ swivel and fixed casters with Total Lock Brakes rated over 1,200 pounds per wheel. Non-marking polyurethane wheels with iron hubs.
- Optional Leveling Feet: Glass-fibre reinforced tube ends and self-leveling swivel stud feet.
- Weighs approximately 1,100 lbs. with legs and casters.
Customizations
- Check out our line of BASE SHELVES, DRAWERS, EXTENSIONS, and REMOVEABLE COVERS.
- For fixturing and productivity, check out our: RISER BLOCKS, FAB SQUARES, and SUPER SLOT ACCESSORIES.
- Need a splash of color and some anti-rust protection, check out POWDER OPTIONS
- Need a custom height table (standard top is 38″)? Check out Custom Height (Cut To Order)
Welding Table Components
Complete tables are built from dozens of laser cut parts, which is just one key component to the overall accuracy of the finished product. Sure, our CNC machines can maintain accuracy to within .002″, but let’s face it – a stack of parts isn’t going to perfectly fabricate itself!
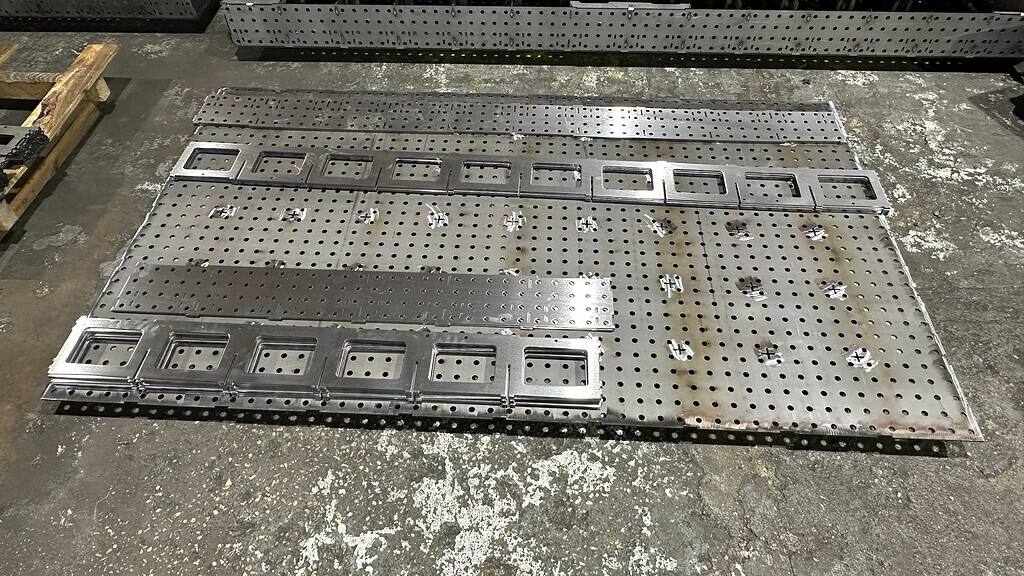
Welding Table Construction
Read our full article: How We Build Super Flat Welding Tables
The strength of a Texas Metal Works weld table comes from the interlocking series of ribs supporting the surface. These precision cut ribs lock together and also interlock with the table surface.
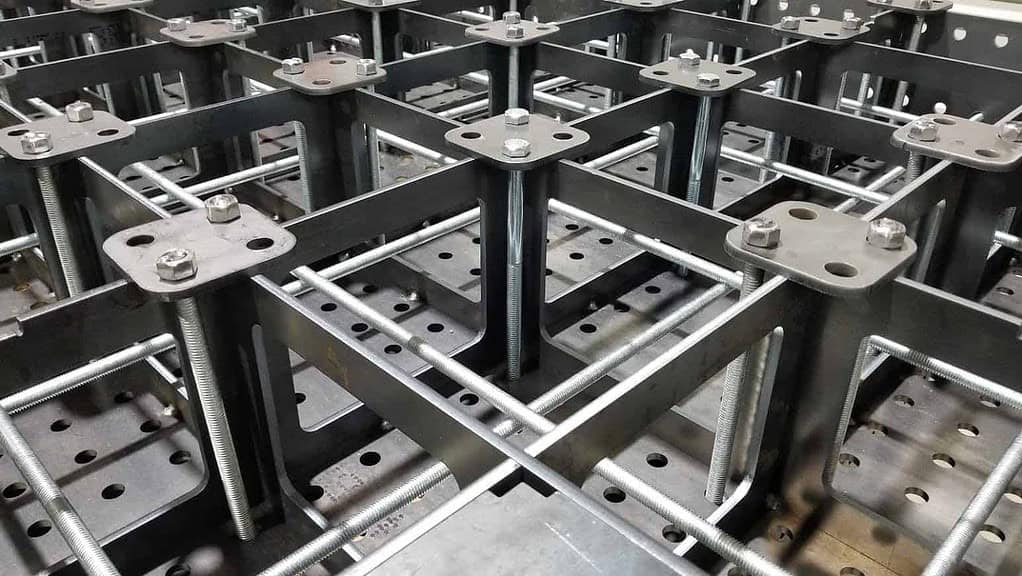
As you might guess, fabricating a huge table with precision requires extraordinary effort and a lot of practice. But we also augment our fabricator’s experience with the best tools available. In addition to using 142 bolts, 132 feet of threaded rod, 63 fixturing plates and making hundreds welds – we also fabricate all of our table on a heavy duty milled reference surface!
You can read a complete discussion of our welding table build process here, but the short version is that we start out by securely bolting every table top directly to a precision milled surface.
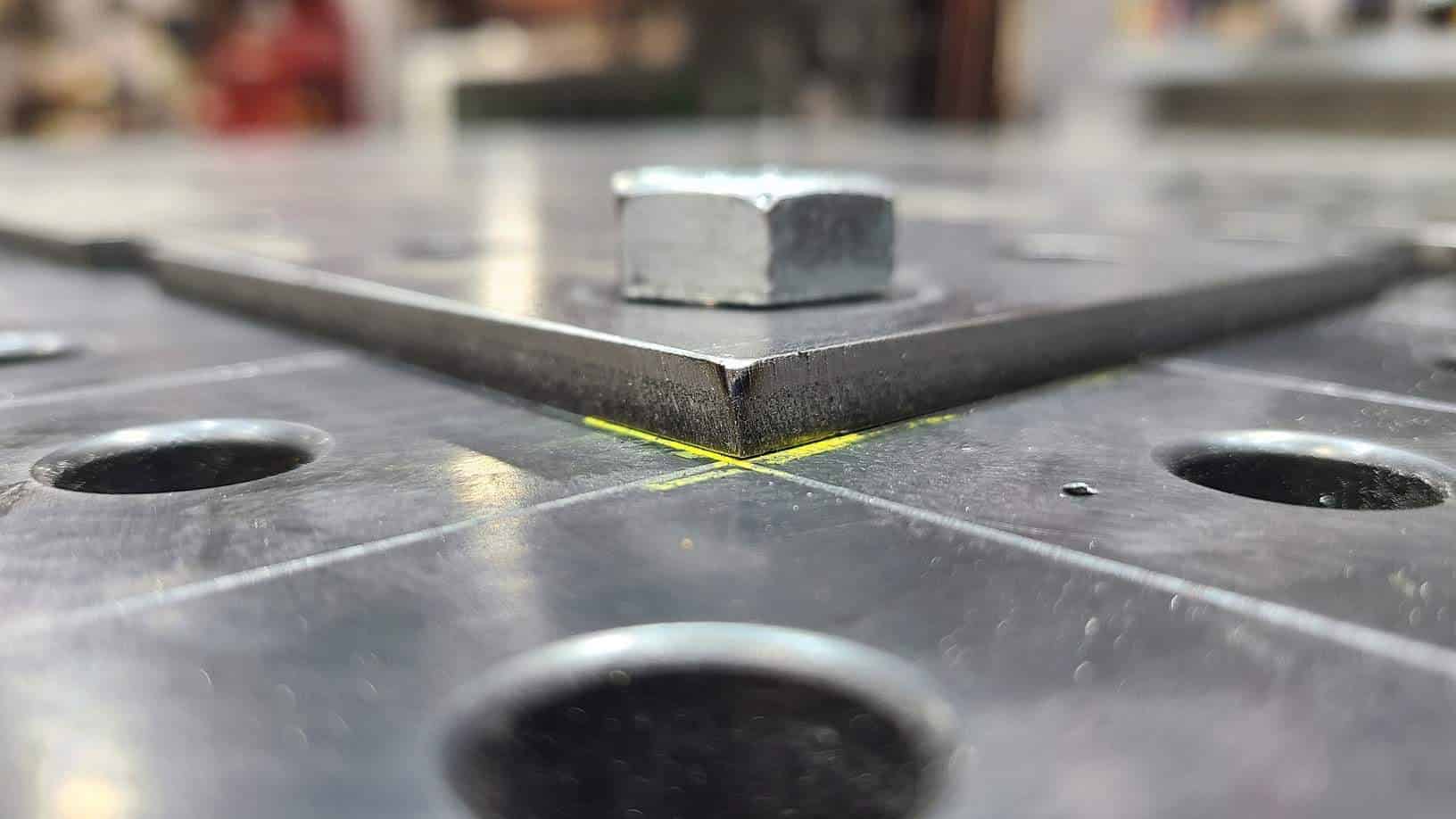
Only after securing the top to a reference surface do we add the ribs and sidewalls and secure them by bolting everything firmly in place before locking it in with hundreds of weld points.
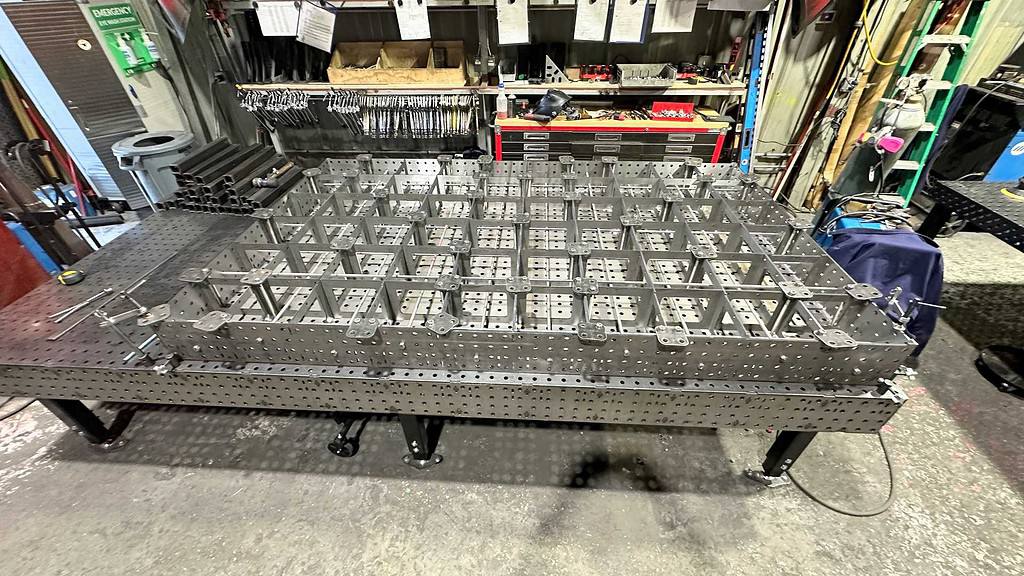
At the end of the day, we’re not happy until we can lay a level across the surface and visually verify that there is almost no (or none whatsoever) daylight peeking through.
Related Information
- How to Keep Welding Tables from Rusting.
- Accessories that work well with our welding tables.
- Understanding welding table flatness.
Notes on Shipping
As you can imagine, these massive tables can be a little challenging to ship and receive. When we ship any of our tables the carriers require us to put them on a pallet. But normal pallets won’t work, so we manufacture custom skids specifically for shipping these bad boys.
Each table is bolted directly to a custom skid with heavy duty hex head screws to ensure it stays put during transport. If you choose the option with casters they’ll be placed in a box and safely strapped to the skid.

These skids are then loaded onto a truck at our end via forklift, and we use long fork extensions to put them in the truck from the end of the table. Shipping companies only carry a small pallet jack on the truck, and those jacks absolutely can’t move these tables. So on the reverse end it’s going to require a similar setup for unloading purposes.
At a bare minimum, you’ll need 48″ forks to lift the table out of the truck. However, we recommend 72″ or 84″ fork extensions. Amazon sells a bunch of extensions in case you need them. We’ve used these 72″ fork extensions to get the job done, and these 84″ fork extensions work even better. When buying forklift extensions pay particular attention to the width of your forks to make sure you get the right size!
If you can get heavier-duty fork extensions we HIGHLY recommend it! Especially if you order your table along with several accessories that will ship on top. The tables plus accessories can often exceed 1,000 pounds, and the light-duty extensions may flex or bend. Please contact us if you have any concerns about receiving, or if we need to make special plans to get things delivered safely!
Lift Gate Not Available
A forklift and/or dock is required for delivery. Most liftgates can handle freight that is equal to or less than 96 inches wide, and 48 inches deep. The weight limit on a standard liftgate is 2500 lbs. Sadly, this table cannot be safely lowered to the ground via liftgate. That said, customers without a forklift or dock will need to identify an alternative means of delivery.
Many of our customers rent a 6×12 Utility Trailer with Ramp from UHaul and transport it to their home/business. Typically, customers will arrange to pick up at the local LTL terminal or ship to neighborhood suppliers (like gas companies). Once there, the supplier can use their forklift to unload the table and the customer can quickly install casters and transfer the table to a utility trailer with a ramp. Upon arrival, the table can safely be rolled off the trailer’s ramp and into their facility!