Hard work. Attention to detail. Pride of workmanship. We’ve got no secrets – we want our customers to know what goes into the tables we build. So today I’m outlining how we build our welding tables, and also importantly why we build them this way. (Note: We have a more recent article about the different methods of manufacturing welding tables.)
What is Flat?
Everyone has a different definition of what “flat” means. And for good reason! Different circumstances demand different degrees of flatness. In fact, here’s an excellent video that breaks down the entire construct of flatness.
If you’re looking for a surface just to put something down, any old surface will do. If you’re looking to build a dining table that doesn’t rock on the floor it’s going to require a different degree of flatness. And if you’re building jet engine parts that spin at 100,000 rpms, you’re going to need a whole different level of flatness!
We can measure each of these different requirements by simply moving the decimal while measuring. For example, a table that is just acting like a shelf might only need to seem “kinda” flat. If it was off by .15″ over every linear foot, over a 10′ span it would only be off by 1.5″. And who cares…. But if we’re building a dining table that’s another story! We need to move the decimal on that flatness over to say .015″ every linear foot. In that case over a 10′ span we’d be out of flatness by about .15″ (about 1/8″). Leveling feet can easily compensate.
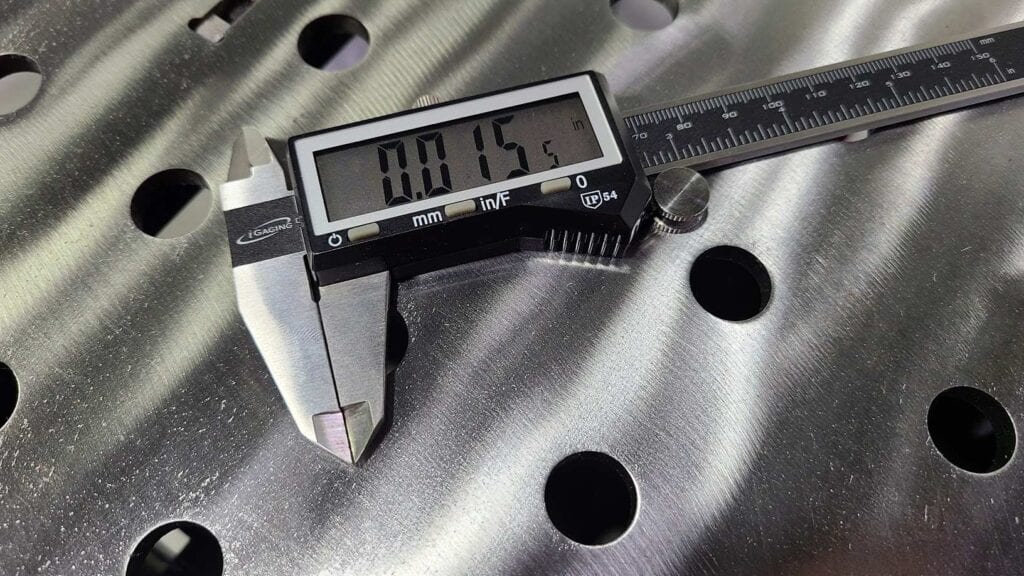
Now on that jet engine, we’re probably going to need to maintain tolerance at least one more decimal point over (maybe 2)! So we’d shift the requirement to .0015″.
Be aware! Companies quoting DIY kits with flatness claims in the .00X range are quoting the specifications of the CNC machine the material is cut on! This is only one of many factors in achieving overall flatness when actually fabricating a table.
The Cost of Flatness
If achieving this level of flatness were easy, everything would be Jet-engine-flat! But the problem is that moving the decimal generally doubles the price for each decimal. So the price will escalate at a rate that looks something like this:
- 1″ Tolerance = $1
- .1″ Tolerance =$2
- .01″ Tolerance = $4
- .001″ Tolerance = $8
- .0001″ Tolerance = $16
We can see this reflected in the prices of welding tables. A homemade welding table might cost a few hundred dollars, stepping up to a professionally built table would double the cost, and further moving up the stack to a fully CNC machined surface would easily double the cost again.
How We Build Tables
The ultimate welding table would be super light weight, super strong, and super flat! For example, if we could machine a solid block of titanium with the world’s most precise milling machine it would be amazing! It would also cost a fortune! But let’s assume something like that is the goal. Here’s how we’re tackling it…
We start out with a precision laser cut kit of parts, we clean and inspect every single part, and then we bolt the surface of our kit directly on a super-flat milled surface!
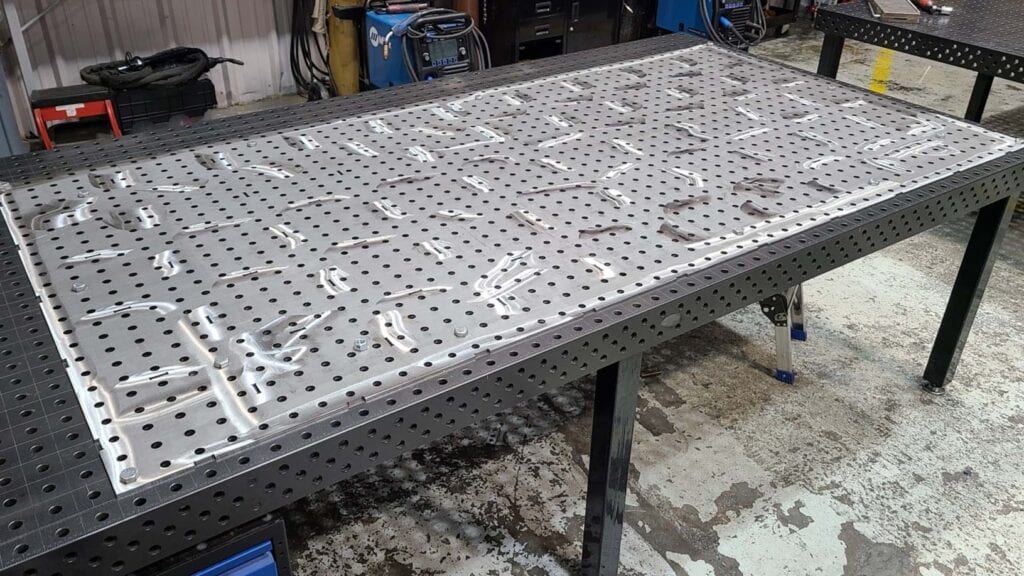
The problem with flat steel plate is that it’s never actually flat. I mean, again, it all depends on your definition… but for our purposes we need to overcome the steel’s memory of being rolled into a coil when it was cast at the mill. When we first lay a sheet of material on the reference surface you can visibly see the difference in flatness.
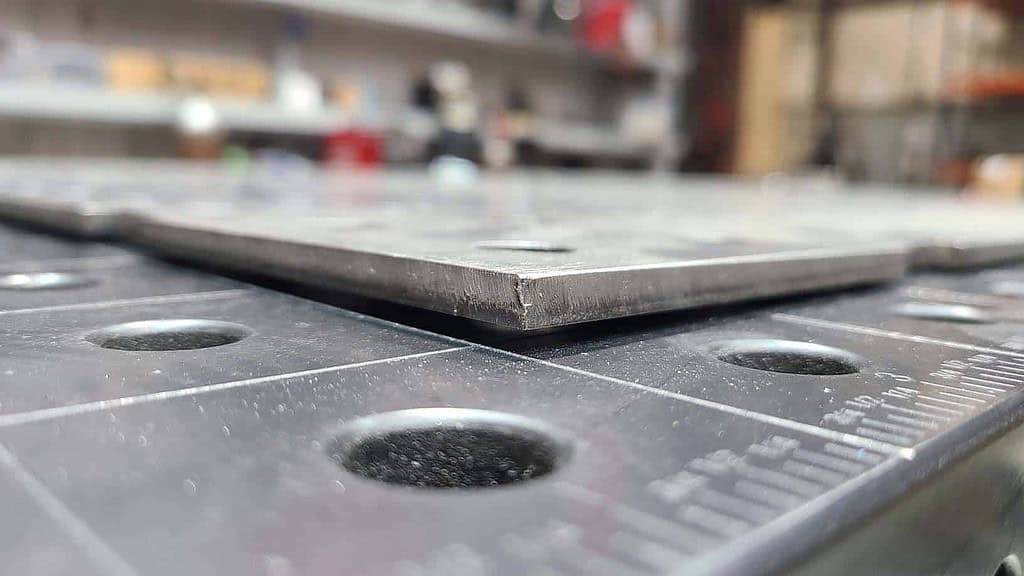
Once we bolt it down to the super flat reference surface we’ve completed the first step in ensuring the flattest possible outcome.
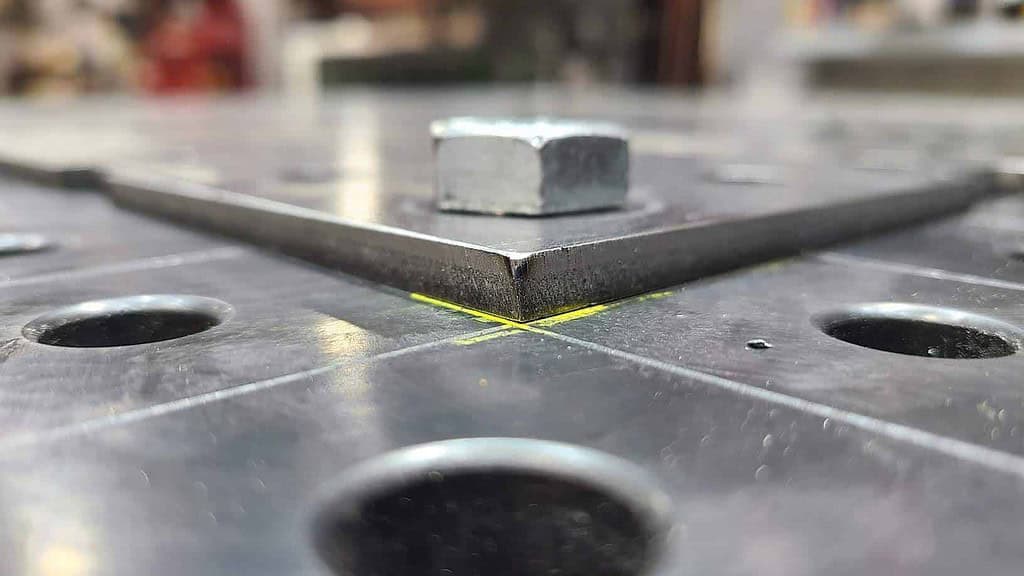
Next we install the series of intersecting ribs that will add strength and ensure we retain flatness. Since all of the parts for our table kits are cut on a CNC laser, we can treat them as additional reference surfaces since the laser maintains accuracy to within a few thousandths of an inch. We formerly relied on this fact to assemble our tables, because if you squeeze the surface against the ribs it will get as flat as the ribs.
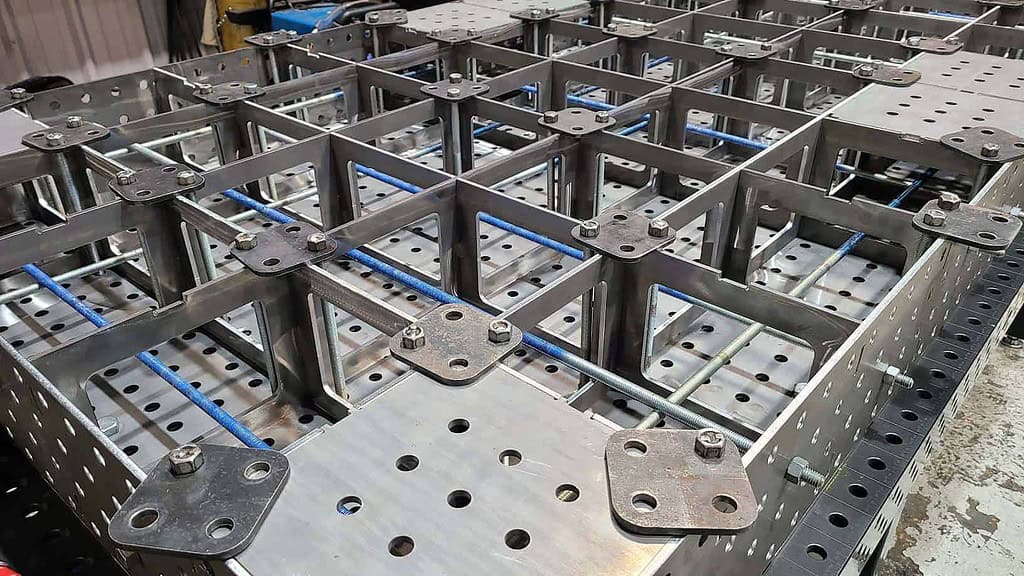
However, now that the new table top is bolted to a known flat surface, when we squeeze the ribs down onto it if there happen to be any gaps they get locked in place when we weld. Which leads me to one other point – when we do the welding, we place 8 small welds in each 10″ square section of table. So on a 50″x100″ table such as the one in the photo above, there will be over 400 welds holding everything together once it’s all said and done.
The end result of all this work is that we end up with a table flat enough that when we put a level across the top you can’t see any daylight under it.
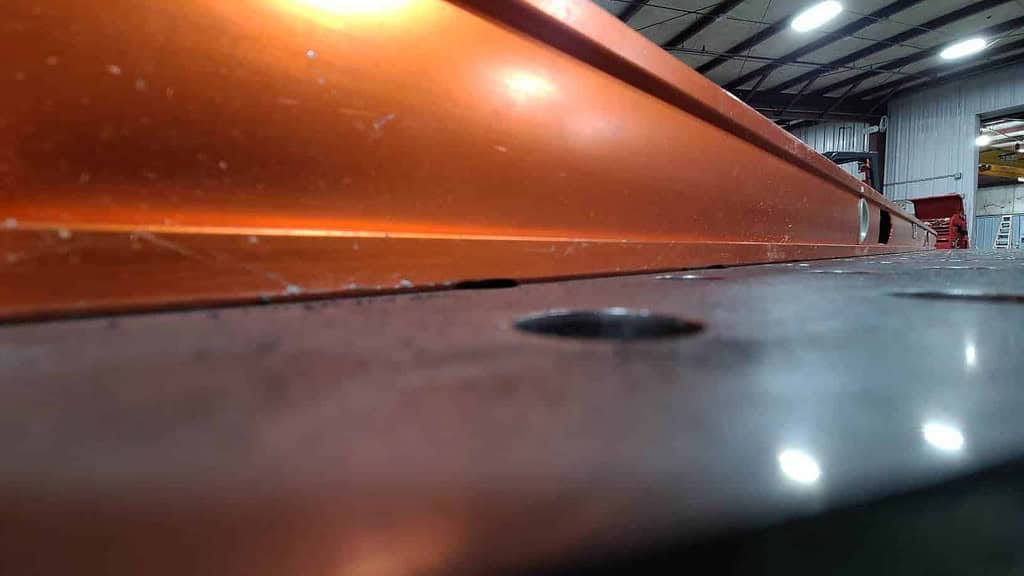
Maximizing the Value Equation
By following this process we’re taking a human assembled kit which could otherwise only achieve a certain level of flatness, and supercharging it by integrating a known reference surface into the equation. It gives us several benefits:
- Less material is required than to cast and mill a similar sized table.
- Easily less than half the weight of a similar sized milled table.
- Can be mounted on heavy duty casters and still have plenty of capacity for a ton of stuff on top.
- Nearly as flat as a milled surface, for a fraction of the cost.
In chart form, these benefits look kind of like this:
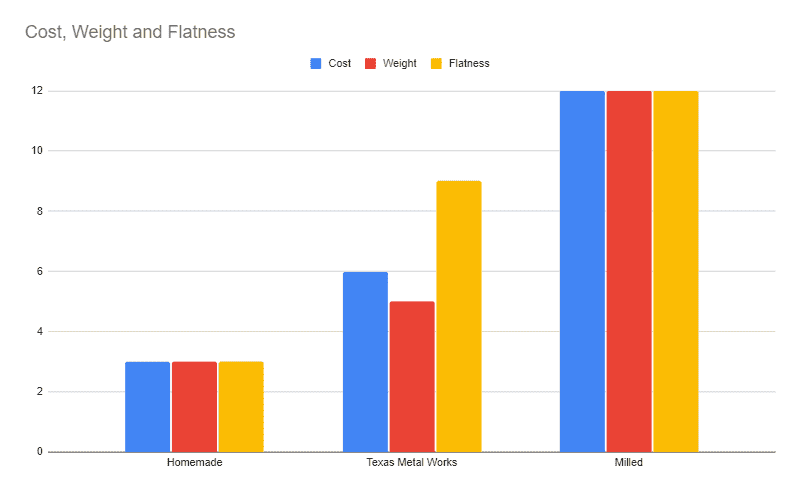
The Bottom Line
We don’t make guarantees about the flatness of our tables because we aren’t actually machining the surface to a certain tolerance. And from inch to inch there will be more variability than a surface that has been precision milled. However, in 99% of all applications we’ve seen, our tables are vastly superior to anything else our clients have been using in the past – and we’ve provided tables to space agencies, the federal government, universities, high schools, corporations and individuals all over the US and internationally.
We match our tables with the absolute best casters and accessories we can find, and we back up everything we sell with our commitment to honesty and integrity at every level through our organization. And at the end of the day, everyone here at Texas Metal Works takes pride in knowing that the tools we build help others build some of the most interesting things on Earth (and beyond)!