We’re super excited to introduce our newest product line! After being asked way too many times if we offer welding booths to go along with our welding tables, we’re releasing a fully modernized, new and improved kind of Welding Booth. They go by the name ModPro, because unlike every other welding booth in existence, ours can be deconstructed and reassembled in different sizes an infinite number of times! This also makes it incredibly simple to expand your system at any time.
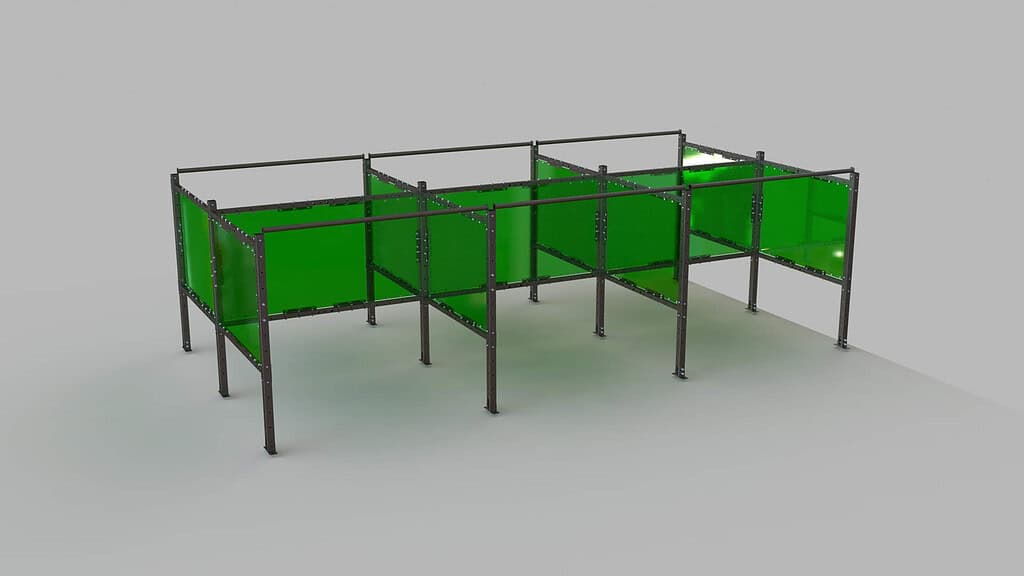
TLDR Version
Our welding booths:
- are 33 times stronger than normal welding booths.
- can be taken apart and reconfigured like you’re working with Legos.
- offer hundreds of laser cut holes for accessories and expansion.
- can accommodate wiring, tubes, etc. running through the frame for organization and protection.
- are less expensive than “competitive” offerings.
For those who are looking to really learn a lot more about these welding booths, here’s a Table of Contents so you can jump ahead, or simply keep scrolling along until you either learn something, or fall asleep. As always, feel free to contact us with any additional questions or needs.
How ModPro Welding Booths Work
We designed ModPro around a standardized set of components which can be mixed and matched to build whatever you want. The primary components are as follows:
- Columns – The basic uprights that support the structure are all cut from 3″ square tubing. This is ridiculous. Kinda. (I’ll explain later….)
- Cross Braces – These span between columns and support wall panels, and anything else we want to hang in there.
- Wall Panels – We offer steel, or a welding rated polycarbonate see-through panel.
- Adjustable Feet – Our standard welding booth height is 7′, but if you need more these will bump it to 8′.
We don’t just cut our tubing to length, it’s all 100% CNC laser cut. And since that’s the case, we absolutely riddle them with holes! Because as I said before, we intend to mount things on them.
We will be introducing a wide range of accessories to bolt to or interact with the welding booths including:
- Top Mount for Fume Extractor
- Accessory overhead lighting
- Accessory shelving
- Super Slot Panels & all Super Slot accessories
- Booth Mounted Worktop
- Steel Workbench
- Fabrication Tables
Hopefully it’s starting to make sense why we don’t want to rely on wimpy 1″ tubing. But let me really, really explain.
Rationale for Engineered Overkill
As previously noted, the tubing we use for our columns is 3″ square, and our cross braces are 2″ square. This is in contrast to the industry standard of 1″ tubing. During development several people told me that the columns were “unnecessarily strong” for just holding welding booth panels. And yes, that would be accurate, if that was all the columns were meant to do. But it’s not.
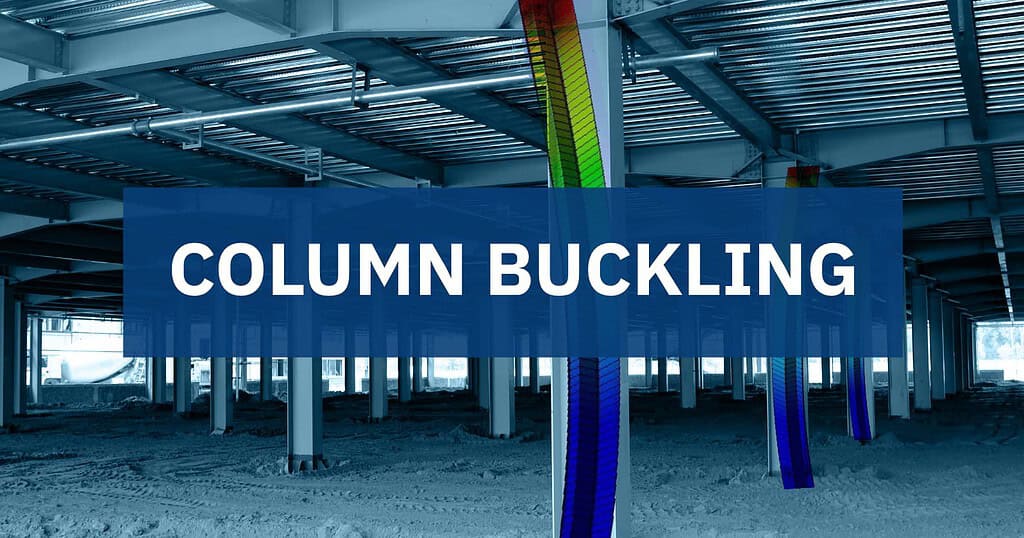
1″ vs 3″ Square Tubing (Nerd Talk)
We didn’t just arbitrarily decide to use crazy oversized tubing. It was a purely mathematical decision, and personally I don’t think it can really be argued. Other companies use 1″ tubing for their welding booths, and that’s fine… as long as you’re not trying to use them to support heavy loads. As soon as you try, you’re increasing the risk of a catastrophic failure by about 33 times.
Load-Bearing Capacity
Euler’s Buckling Formula: For long columns, the load-bearing capacity can be estimated using Euler’s formula:
Pcr = π2EI /(KL)2
- Where Pcr is the critical load,
- E is the modulus of elasticity of the material
- I is the moment of inertia
- K is the column effective length factor
- L is the length of the column.
Since the moment of inertia I increases with the fourth power of the dimension, the load-bearing capacity of the 3″ tubing will be significantly higher than that of the 1″ tubing.
The Proof
Here’s the proof. For square tubing with side length b and wall thickness t, the moment of inertia I is given by:
I=b4/12 − (b−2t)4 / 12
Assuming a wall thickness t=0.1″:
For 3″ square tubing:
I3" = 34/12 − 2.84/12 ≈ 81/12 − 61.4656/12 ≈ 6.75 − 5.122 ≈ 1.628 in4
For 1″ square tubing:
I1" = 14/12 − 0.84/12 ≈ 1/12 − 0.4096/12 ≈ 0.0833 − 0.0341 ≈ 0.0492 in4
The Final Calculation
Using Euler’s buckling formula, the load-bearing capacity is proportional to the moment of inertia I:
Load Capacity Ratio = I3" / I1"
Substituting the calculated moments of inertia:
Load Capacity Ratio = 1.628/0.0492 ≈ 33.08 TIMES!!!
33 Frickin’ Times Stronger!!!
You read that right. The 3″ square steel tubing has a load-bearing capacity approximately 33 times that of the 1″ square steel tubing, given the same wall thickness and material.
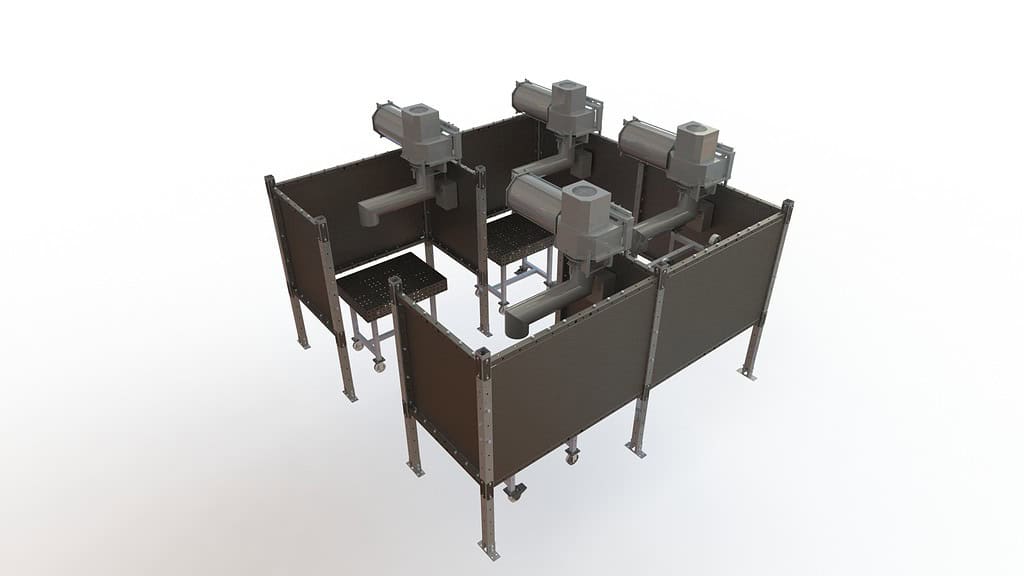
The reason we really care is because if we bolt a fume extractor that weighs hundreds of pounds above someone’s head, I don’t want to HOPE nothing bad will happen. I want to PLAN in advance for it and take precautions. Yes, a 1″ tube will hold a lot of weight if the load is only vertical. But what do you think happens if a forklift accidentally clips one of the legs??? When it buckles, the other legs aren’t strong enough to take up the load and the whole thing comes down on whoever is nearby.
That’s not how we roll.
On Modularity
In addition to the absolute strength of our welding booths, one of the other great benefits is that at any time you can just order some extra parts and bolt them onto your existing structure to grow and expand it.
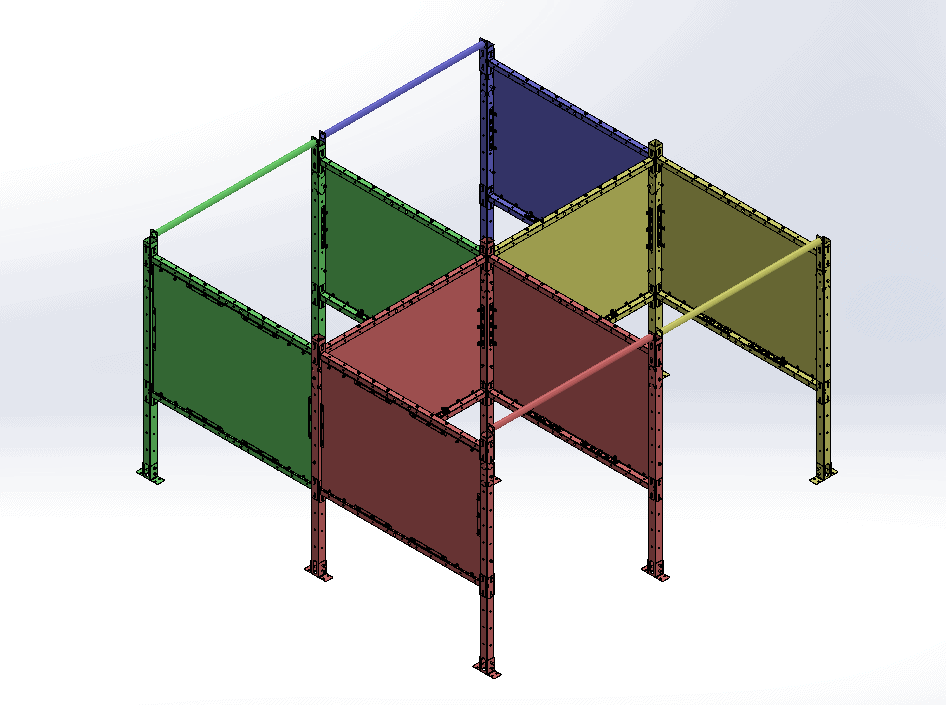
Our little illustration here gives you an idea of how this might work:
- Phase 1 (Red) – You set up a single booth because you only need one station.
- Phase 2 (Yellow) – You decide to expand in a row. For your second station you only need 2 columns and 2 panels.
- Phase 3 (Green) – You add another station. Same deal, 2 more columns and panels.
- Phase 4 (Blue) – What the heck, you go for the Quadfecta because it only takes one column and panel!
In addition, each of our columns and cross braces has dozens of laser cut holes that allow anything you can imagine to be attached.
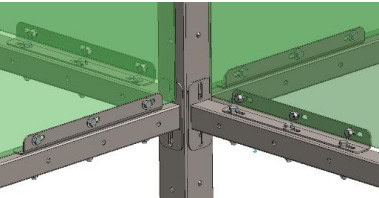
We will be releasing a bunch of special accessories to compliment the weld booths, such as overhead lighting, shelving, Super Slot Panels and more. But if you need something specific just let us know and we’ll make it! Chances are, if you need it others will too.
OSHA Compliance and Enhanced Safety Features
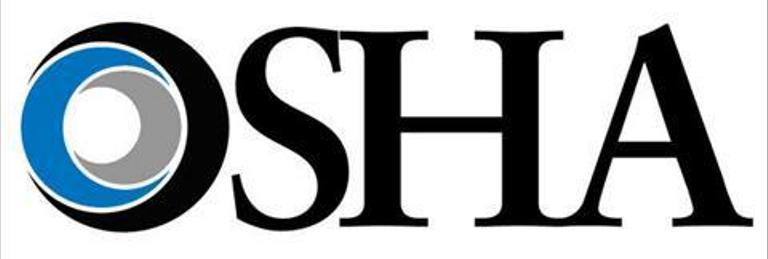
Our welding booths aim to not only meet, but exceed OSHA’s standards for welding environments, addressing comprehensive health and safety concerns. This includes adherence to specific OSHA regulations:
- Fume Extraction: Our integrated fume extraction systems efficiently remove harmful welding fumes and gases from the work environment. This feature supports compliance with OSHA’s requirements for ventilation to ensure air quality, as outlined in standards such as OSHA 1910.252(c)(2) for general requirements in welding, cutting, and brazing
- Vision Safety with Tuffak WC: Incorporating Tuffak WC panels in our welding booths provides critical protection against UV radiation and the intense light produced by welding arcs. This aligns with the need for protective measures against optical radiation as per OSHA standard 1910.133(a)(5), safeguarding the vision of both operators and bystanders and reducing the risk of eye injuries.
- Fire Safety and Protection: Constructed with materials rated for welding applications, our booths minimize fire hazards, in line with OSHA’s fire prevention strategies, particularly those detailed in OSHA 1910.252(a)(2)(iii) regarding precautions for fire prevention.
- Design and Customization for Safety: Our booths are designed to accommodate additional safety equipment and accessories, promoting an organized, efficient, and safe workspace, adhering to OSHA’s housekeeping standards for welding areas.
Where to Get Them
We have multiple variations which can be ordered on our website.
- Stand Alone Welding Booths – If you just need one welding booth. Or you want to place booths in different locations.
- Side By Side Welding Booths – If you would like a row, with shared walls (saves a bunch of money)
- Back to Back Welding Booths – If you’d like two rows, facing opposite one another sharing back walls
- Individual Components – For expansions and replacement parts