One of the routine discussions I’ve had with clients over the years centers around welding table thickness. In the “old” days, welders would take a nice thick piece of material, slap some legs on it, and earn bragging rights simply by how thick your top was! If you had a 2,000 pound, 1″ thick slab of steel, that was great!
But those old mantras don’t apply to modern fixture tables, and certainly not the ones we build at Texas Metal Works. Instead, we’re focused on strength, flatness and precision. I previously discussed flatness in detail, so we’re not going to go into that. Instead, we’re talking about whether or not it’s necessary to offer a variety of table thicknesses, and why.
Yes, We Can!
Let’s get this out of the way. We CAN, and WILL make any of our welding tables with tops of any thickness a client wants. You want 5/16″, 3/8″, 1/2″? YES, YES, YES! Now that we’ve got that out of the way, lets drill down and try and figure out if it’s worth it…
Is it Flatter?
It’s no secret how we build our tables. We fixture up all of the pieces using bolts, plates and threaded rods to squeeze everything nice and tight! Since we cut the support ribs on a CNC laser, we know they are extremely flat. Thus, when we take the slightly curved top plate (because ALL steel is slightly curved or wavy) and clamp it against the straight rib, we expect it to straighten out to match.
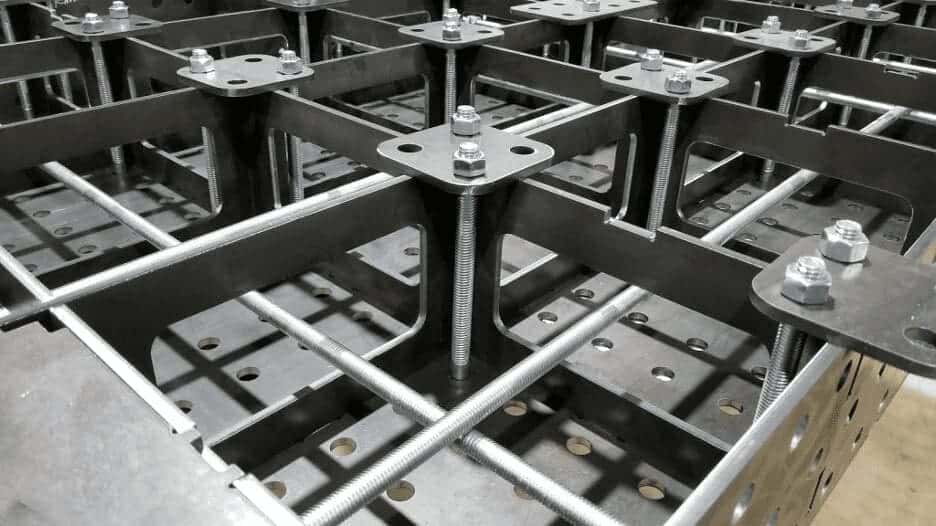
Our standard is 1/4″ plate. But let’s imagine we go with 1/2″ plate instead! Now, we have to fight the natural bow of twice the thickness of steel, which means we have to clamp MUCH tighter to achieve the same result. This also puts the entire table under more stress, and requires much more welding, which also means much more heat input, which means more expansion and potential for deformation.
In other words, the thicker the plate goes, the more difficult it is to get it super straight. This isn’t just for us… it’s for anyone who is undertaking the task of building a super flat surface!
Unforseen Complications
If we build a table with thicker material, we only use the thicker material on the top. There is simply no reason to waste it on the sides or the supporting ribs. Now that’s not really important, but just something to note. And here are a couple of things to consider. This is a rendering of our 60″x120″ welding table.
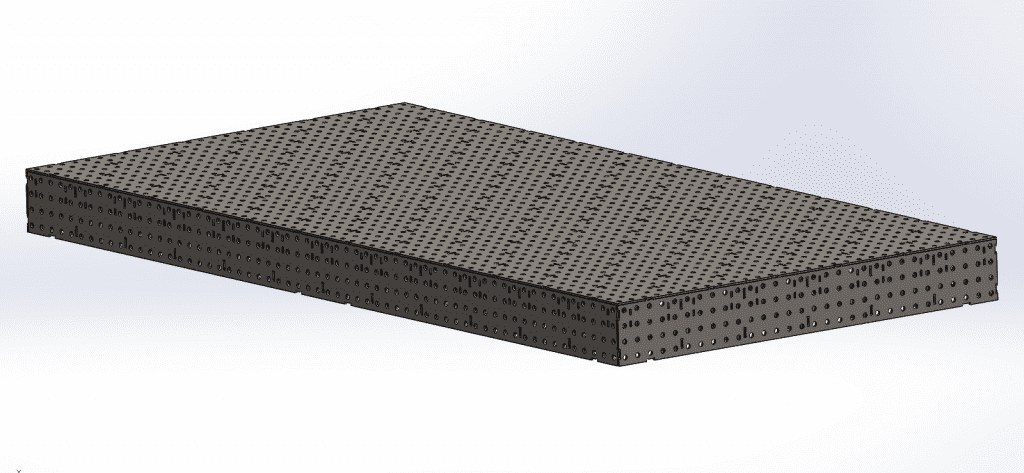
Just the top of this table (meaning not including the legs and casters) weighs 932 pounds when cut from 1/4″ steel. If we upsize that to 3/8″ the weight swells to 1225 pounds. That 293 pound difference comes into play by making the table that much harder to roll around, and by permanently subtracting that weight from the total the casters can support in terms of material you would otherwise be able to put on the table.
Another detail you might not catch is that ALL accessories are designed out of 1/4″ material. Here’s a little closeup of the table with a 3/8″ top on it. Note how the top sticks up where the tabs and slots are? That extra material means that if you were to add a vise mount, or a table extension, the surface of those accessories would be below the table surface.
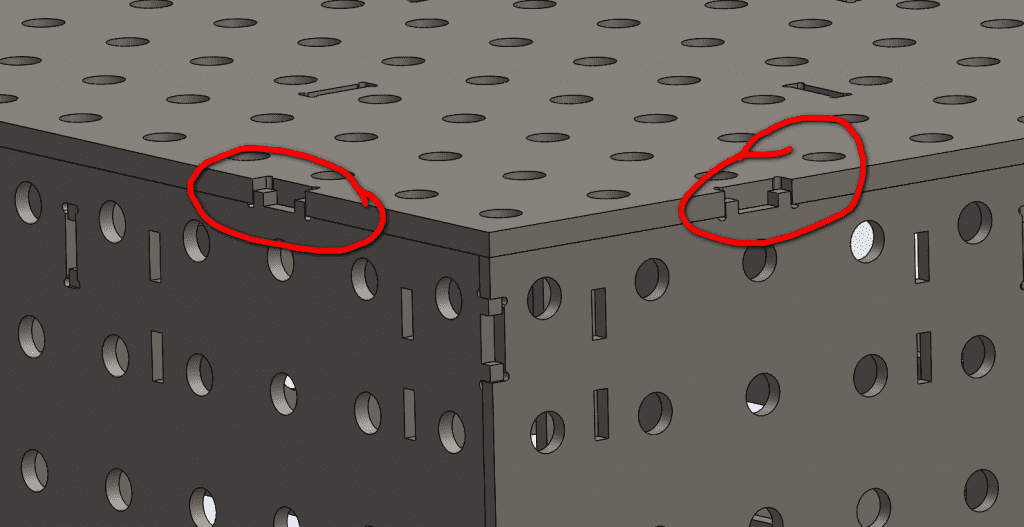
Oh, we can make you custom accessories to match a thicker table top if you want! And we absolutely will too! But it’s going to also cost quite a bit extra.
NOTE: We solved the issue of using accessories with thicker tops by employing slots instead of holes for mounting. Now they can move up and down to accommodate any thickness. 🙂 You’ve have thought we’d figured that out immediately, but sometimes the simplest solutions elude you the longest.
Is it Stronger?
Our tables have either 6″ or 8″ ribs and sidewalls in criss-crossing, intersecting patterns that support the top of the table. You can think of every intersection as a column of steel, and it’s this infrastructure that gives the table it’s rigidity and strength!
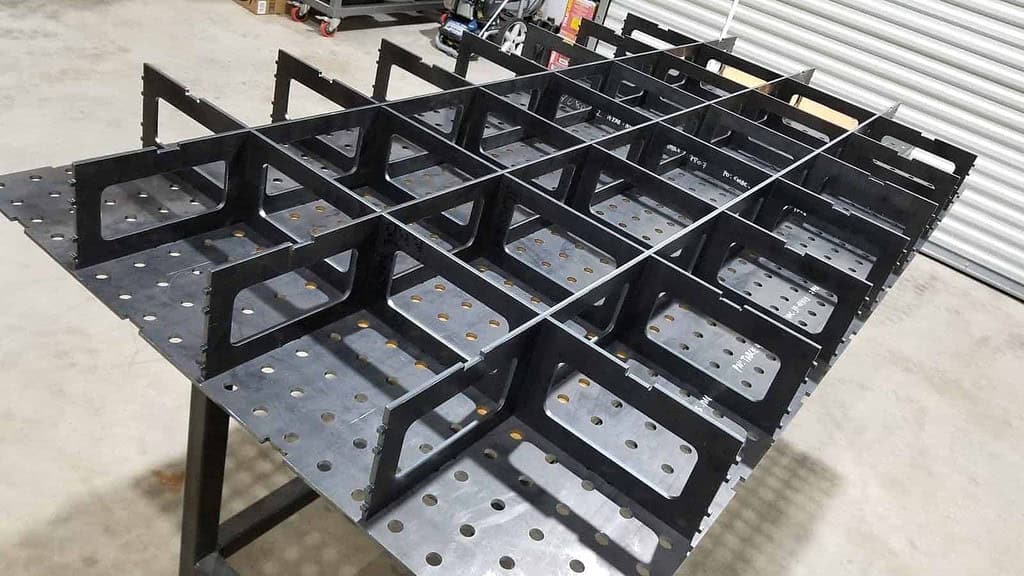
If you took a piece of 1/4″ steel and hung it off the edge of a cliff and jumped on it, it would probably spring like a diving board. But so would a piece of 3/8″, or even 1/2″ – though not as much. But if you put any of them on top of the rib infrastructure above, there simply isn’t going to be a spring. It’s going to be rigid.
So is it stronger? Well, if you add more steel to something, sure! But is any of that usable or necessary beyond what you’d already have? Most likely the law of diminishing returns comes into play.
Is it Tougher?
In this video, at 41:06, Jason from Fireball Tool performs a test in which he takes the biggest clamp he can find and cranks it against a hole in a Certiflat table to the tune of over 1,000 lbs of force. He then rubs his finger over the hole and feels what he described as edge deformation.
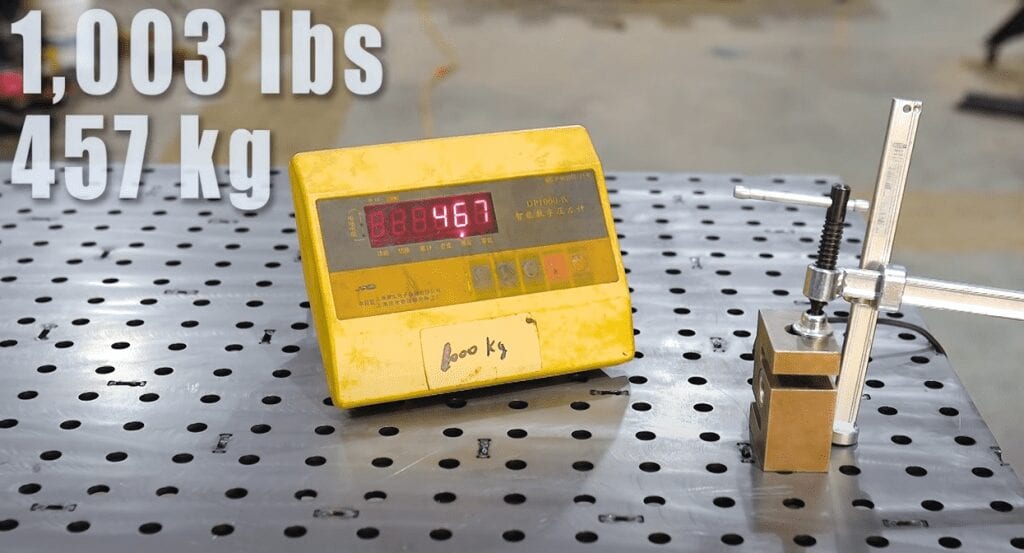
Although this part of the nearly hour long video lasted only about 10 seconds, without any detailed view of the damage done by the tool, I’ve had a number of customers who have worried about thickness of table tops as a result. So let’s break this down…
- You can watch the video 100 times and pause it on every frame, but you can not see the damage Jason felt with his finger. It would have been measured in thousandths of an inch. If every hole on the table suffered the same damage, a level would still lay almost perfectly flat across the surface of the table.
- If you’re concerned with thousandths or even hundredths of an inch on your welding table, you’re looking at the wrong tables to start with. You need to pony up $12,000 for a 5,000 pound plus cast, milled table. These are not the droids you’re looking for…
- He was bending the actual clamp by exerting so much pressure, almost to the point of failure. No one is EVER going to need to clamp anything to one of these tables with that much pressure. If so, you’re doing it wrong. Also, instead of a clamp that pushes on the side, just use a bolt that pulls straight down!
- Finally, here is a photo where I used two BuildPro 6.5″ InsertaClamps to pick up one of our 1,000+ pound 50″x100″ weld tables. These clamps are only rated at 300 pounds each.
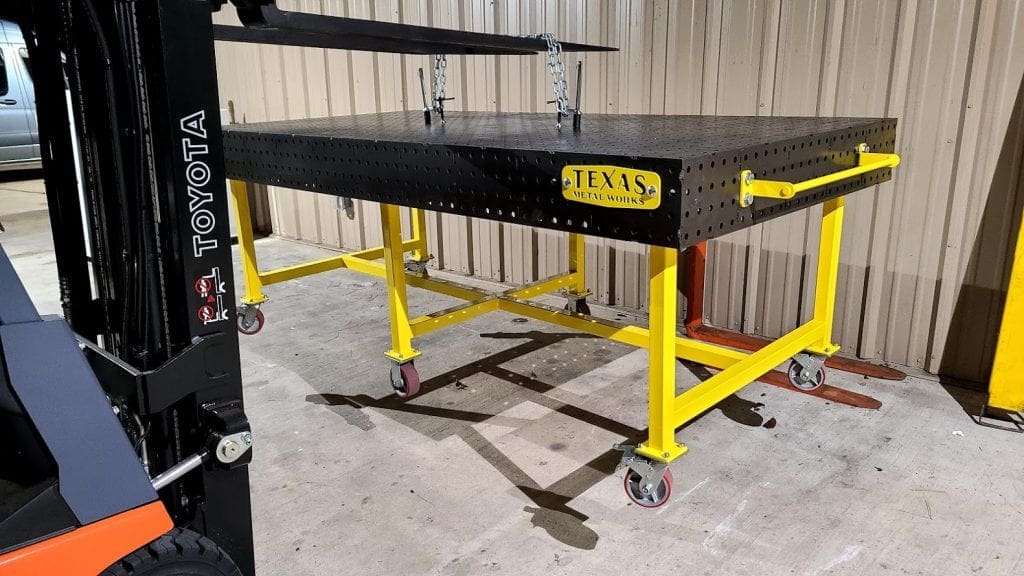
It’s safe to say that these clamps are WAY beyond their rated capacity. And it’s also safe to say there is absolutely no need for them ever to be putting this much pressure on holes in that table top. Ever.
Now, here’s a closeup of the clamps with the table hanging in the air.
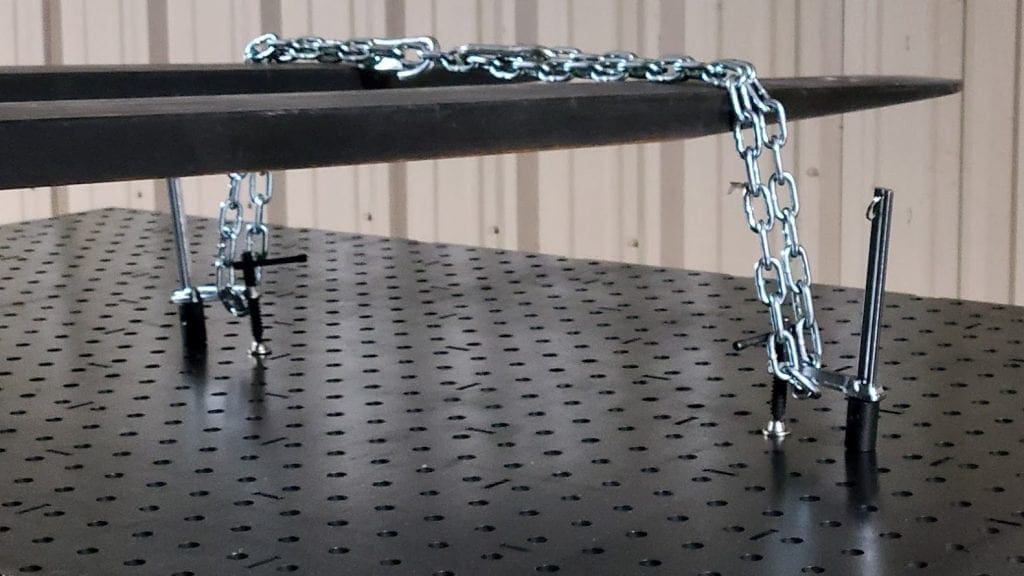
And here’s the exact hole the right clamp was in immediately after letting the table down. There was no edge deformation easily visible or that I could feel with my finger, despite having suspended at least 500 pounds in the air.

I also took a macro photo to see if I could catch ANY damage to the hole, and here is the photo.
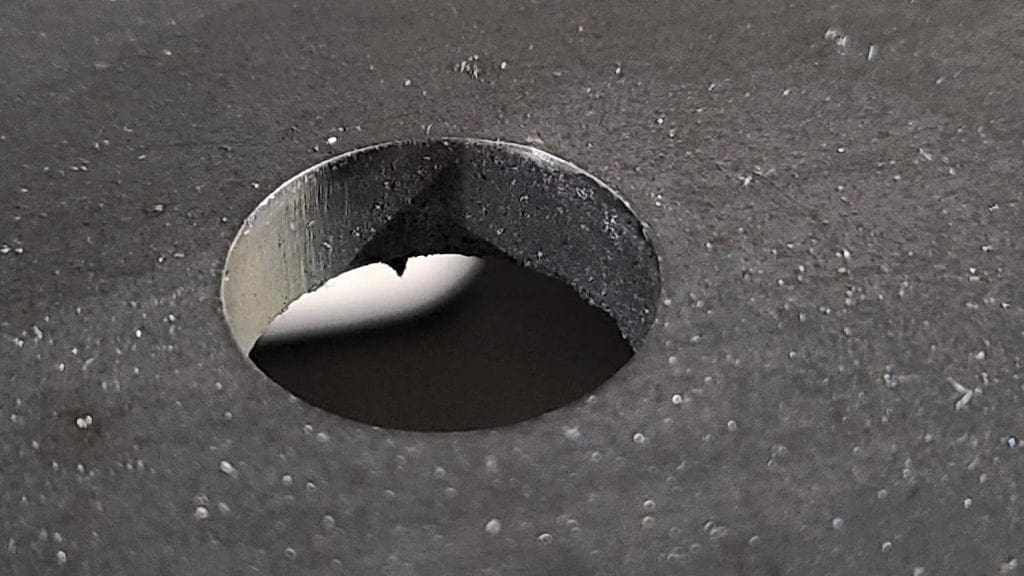
Can you spot that tiny, tiny little indentation at about 1 o’clock in the photo? It’s only at the very, very edge, and tooling in the hole is unaffected. This could even be from a previous event. And it also isn’t enough to really even feel. The dirt on the table is easier to feel, and a weld BB getting stuck on the edge of, or inside a hole is much worse. So why was Jason able to feel his deformation and file it down so easily?
Following is a comparison between the Bessey and BuildPro clamps that we see in his video, and my photo above. The image angles are not exactly the same, but it appears the Bessey is leaning at a greater angle. This could be caused by a few things:
- 1,000 lbs of force!
- The certiflat holes could be cut slightly too large, allowing the tool to lean more than necessary and do extra damage.
- The Bessey clamp could be undersized slightly, fitting too loosely in the holes and doing extra damage.
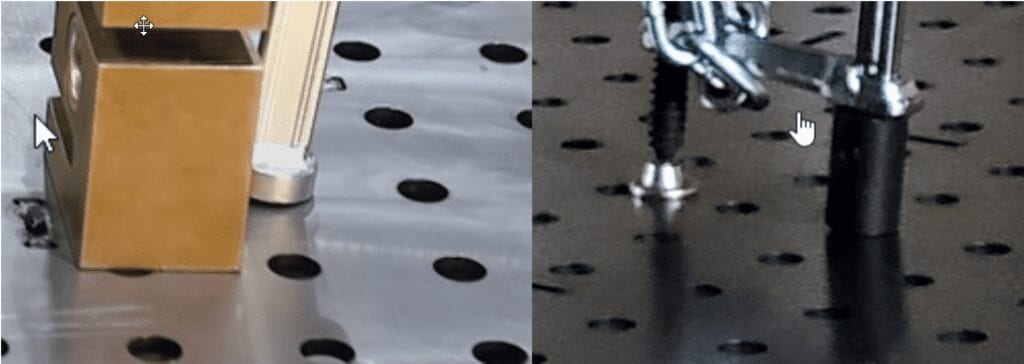
Now, the question is, would a thicker table top have performed better? Well, here’s a 3D model (to scale) demonstrating the difference between .25″ thick material and .375″ thick material, with two holes sized at .63″ and two cylinders of .625″ inserted.
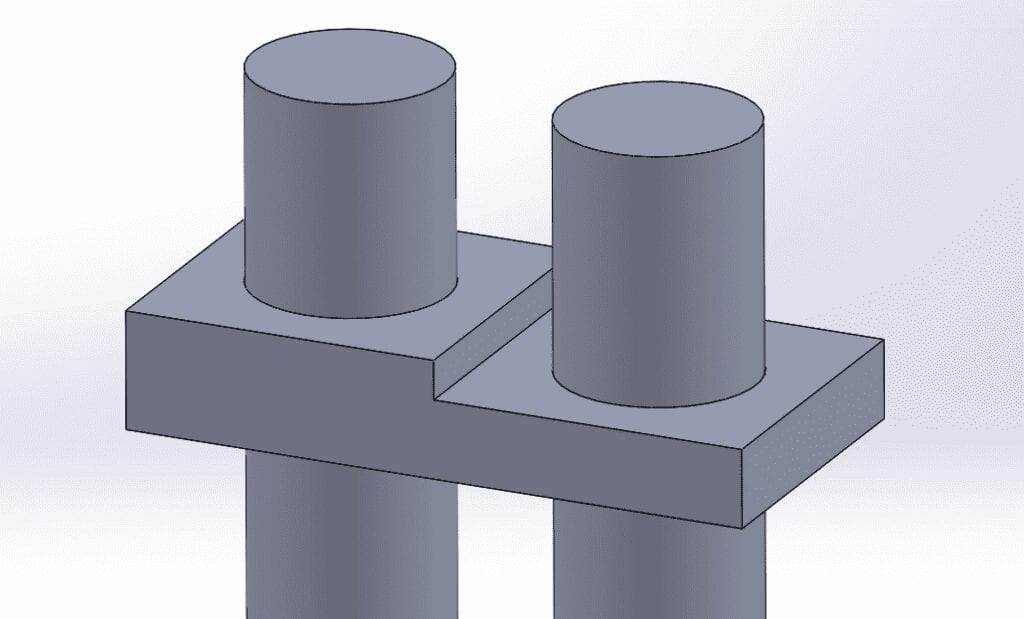
Assuming tooling is accurately sized, there’s only approximately a .005″ gap for the cylinders to move around in the hole. So the difference between the angle a tool would lean through .25″ and .375″, respectively, is a tiny fraction of 1 degree. Not enough to protect the hole from damage in the case of outright abuse. In other words, if tooling is going to deform the edge on quarter inch material, it’s going to do the same thing on a thicker piece.
So What Happens in the Real World?
All of this excessive clamping and hanging tables from forklifts is fun and all, but let’s talk about a real working shop for a moment. We have tables in our shop that have been in daily use for a couple of years, and I can’t find a single hole that feels like the edge has been damaged from tooling. And we make tables! So I guarantee we don’t take as good care of them as our customers! Because the guys in the shop figure we can always make another…
Here are a couple of closeups of random actual holes.
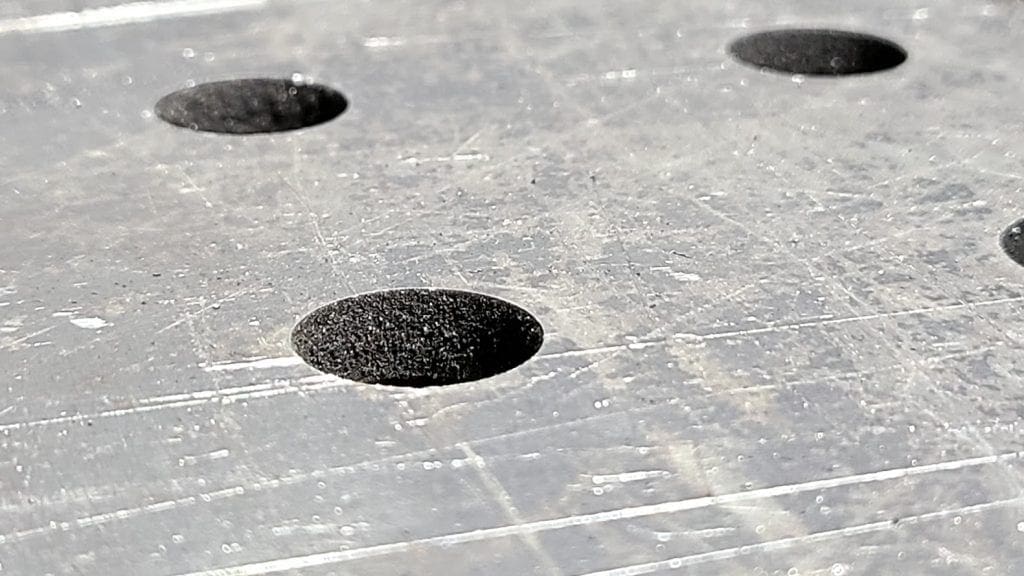
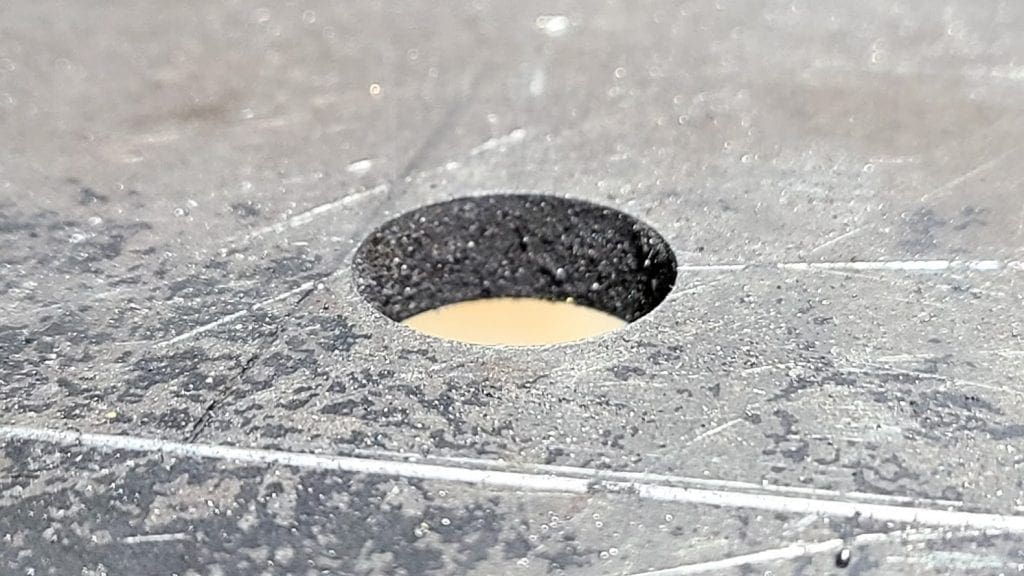
These are just average holes, on a really well used, scratched up, not particularly well cared for table. But they all work great! And at the end of the day, we have to step back and remember, that if we lay a level across this table, it’s still EXTREMELY flat by almost anyone’s definition.
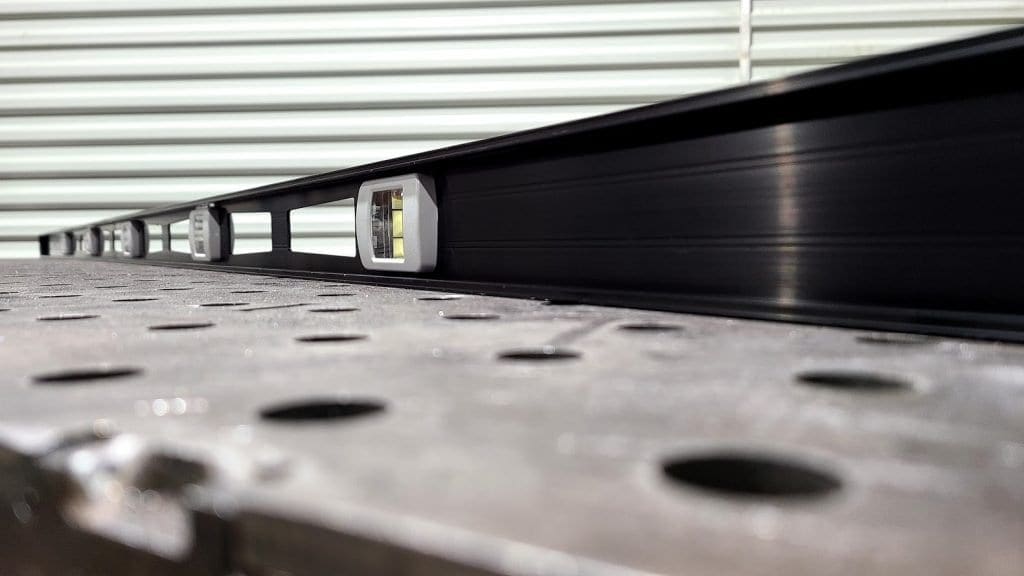
In Conclusion
At this point we come full circle. Are there instances where a thicker table top could deliver demonstrable benefit? Surely there are! The problem is that it probably costs more than the value it delivers.
- The table is no flatter.
- The table will cost considerably more.
- Tooling will not benefit from the additional thickness.
- Usable strength is likely unaffected.
- You probably can’t build anything on a thicker top that you couldn’t on a normal one.
- Accessories aren’t going to work properly. (SOLVED! 🙂
And the last thing to keep in mind is that the guy who would would profit handsomely from selling you a thicker table top, is the one telling you it probably isn’t worth it! But if you want one, just contact us and we’ll cut it for you any thickness you want!!! Guaranteed.